Double-sided double-glass assembly for back contact solar cell, and manufacturing method of double-sided double-glass assembly
A technology of solar cells and back contact cells, which is applied in the direction of electrical components, final product manufacturing, sustainable manufacturing/processing, etc., can solve the problems of restricting the application and development of back contact technology, large front shading area, and low component power, and achieve Good anti-PID performance, low cost and high yield
- Summary
- Abstract
- Description
- Claims
- Application Information
AI Technical Summary
Problems solved by technology
Method used
Image
Examples
Embodiment 1
[0036] Embodiment 1, the manufacturing method of double-sided double-glass modules of back-contact solar cells, specifically: select a piece of low-iron ultra-clear embossed tempered glass as the first glass layer 1, first place the tempered glass horizontally, and make conductive glass on the tempered glass. circuit, and then print or deposit conductive glue on the corresponding position as the conductive medium point, and then place the first packaging material layer 3——transparent EVA, and the first packaging material layer 3 has through holes corresponding to the conductive medium point one by one. The dielectric point passes through the through hole, and then the back-contact double-sided cells are placed. The cells are arranged in a matrix. glass, forming the middle piece, laminating the middle piece, and finally connecting the conductive core board with the junction box 8 through the glass hole with a soldering tape, and bonding the junction box 8 with silica gel.
[00...
Embodiment 2
[0038] Embodiment 2, the manufacturing method of double-sided double-glass modules of back-contact solar cells, specifically: select a piece of low-iron ultra-clear embossed tempered glass as the first glass layer 1, first place the tempered glass horizontally, and then place the nano-silver wire directly Coated on the tempered glass on the back, and then use laser lithography technology to describe and make a transparent conductive film with nano-level silver wire conductive pattern; print or deposit conductive medium points on the transparent conductive circuit, and the conductive medium point position is the same as that of the back contact type The positive and negative electrode points on the back of the solar cell correspond to each other; then place the encapsulating adhesive film on it. The adhesive film needs to punch several through holes in advance. The number of through holes is the same as the sum of the number of positive and negative electrodes of several batterie...
Embodiment 3
[0040] The same as in Example 1, wherein the nano-silver transparent conductive film is that the nano-silver wire is coated and printed, and the mask plate with the opening pattern is close to the surface of the glass, and then the nano-silver is printed on the glass to form a ribbon. A patterned transparent conductive circuit, the distance between adjacent conductive lines in the patterned transparent conductive circuit is between 2mm, the coating thickness is 20 microns, and then baked at 120 degrees for 5 minutes. The printed pattern formed can realize the back contact battery connection between.
PUM
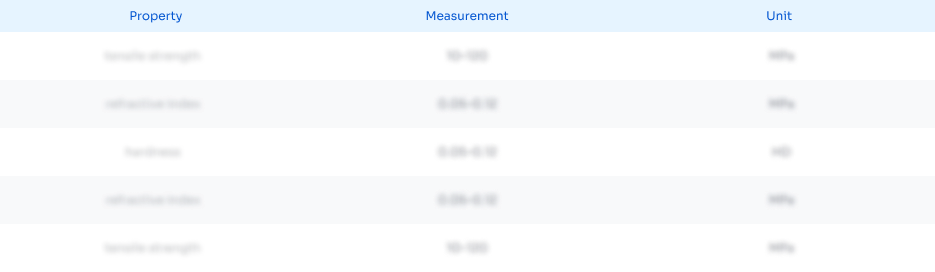
Abstract
Description
Claims
Application Information

- R&D
- Intellectual Property
- Life Sciences
- Materials
- Tech Scout
- Unparalleled Data Quality
- Higher Quality Content
- 60% Fewer Hallucinations
Browse by: Latest US Patents, China's latest patents, Technical Efficacy Thesaurus, Application Domain, Technology Topic, Popular Technical Reports.
© 2025 PatSnap. All rights reserved.Legal|Privacy policy|Modern Slavery Act Transparency Statement|Sitemap|About US| Contact US: help@patsnap.com