Thermo-mechanically-recoverable crosslinked cable material and preparation method thereof
A cross-linked cable and cable material technology, applied in the field of wire and cable, can solve environmental pollution and other problems, achieve good durability, ensure stability, and improve strength and durability
- Summary
- Abstract
- Description
- Claims
- Application Information
AI Technical Summary
Problems solved by technology
Method used
Image
Examples
preparation example Construction
[0025] Such as figure 1 Shown, be the preparation method of the cross-linked cable material that can be recycled by thermomechanical of the present invention, comprise the steps:
[0026] Step 1, chlorinated polyethylene with a Cl% content of 100 parts by mass of 30-45% and methacrylates of 5-10 parts by mass, i.e. methyl methacrylate, butyl methacrylate, methacrylic acid One or both of hydroxypropyl ester or glycidyl methacrylate, and 0.5-1.2 parts by mass of peroxide are kneaded on a kneader at 100-110°C for 8-15min to obtain type A grafted chlorinated polyethylene. The peroxide is one of dicumyl peroxide, benzoyl peroxide or 2,5-dimethyl-2,5-bis(t-butyl peroxide)hexane;
[0027] Step 2, 100 parts by mass of chlorinated polyethylene with a Cl% content of 30-45% and 2-8 parts by mass of vinyl alkanoates, i.e. vinyl acetate, vinyl propionate, vinyl butyrate or hexanoate One or two kinds of vinyl esters and 0.1-0.5 parts by mass of peroxide are kneaded on a kneader at 100-11...
Embodiment 1
[0042] Step 1: 100 mass parts of chlorinated polyethylene with a Cl% content of 30%, 5 mass parts of methyl methacrylate, and 0.5 mass parts of benzoyl peroxide are kneaded for 15 minutes at 100 ° C on a kneader, Obtain type A grafted chlorinated polyethylene;
[0043] Step 2: the Cl% content of 100 mass parts is 30% chlorinated polyethylene and the vinyl acetate of 2 mass parts, 6 mass parts vinyl propionate, and a kind of dicumyl peroxide of 0.5 mass part On a kneader, knead at 110°C for 7 minutes to obtain type B grafted chlorinated polyethylene;
[0044] Step 3: the A-type graft chlorinated polyethylene of 50 mass parts, the B-type grafted chlorinated polyethylene of 50 mass parts, the calcium carbonate of 100 mass parts and 60 mass parts pseudo-boehmite, and 2 mass parts Chloropropyltriethoxysilane, 20 parts by mass of silicon dioxide, 10 parts by mass of carbon black, 1 part by mass of microencapsulated red phosphorus flame retardant, 4 parts by mass of dioctyl phthalat...
Embodiment 2
[0048] step 1:
[0049] 100 parts by mass of chlorinated polyethylene with a Cl% content of 45%, 4 parts by mass of butyl methacrylate, 6 parts by mass of hydroxypropyl methacrylate, and 1.2 parts by mass of 2,5-dimethyl- 2,5-bis(tert-butylperoxy)hexane was kneaded at 110°C for 8 minutes on a kneader to obtain type A grafted chlorinated polyethylene;
[0050] Step 2:
[0051] 100 parts by mass of chlorinated polyethylene with a Cl% content of 45%, 2 parts by mass of vinyl butyrate and 0.1 parts by mass of benzoyl peroxide were kneaded for 12 minutes at 100°C on a kneader to obtain Type B branched chlorinated polyethylene;
[0052] Step 3:
[0053] With 50 mass parts of A-type grafted chlorinated polyethylene, 50 mass parts of B-type grafted chlorinated polyethylene, 150 mass parts of calcium carbonate and 30 mass parts of pseudo-boehmite, and 5 mass parts of chloropropyl Triethoxysilane, 20 parts by mass of silicon dioxide, 5 parts by mass of carbon black, 5 parts by mass ...
PUM
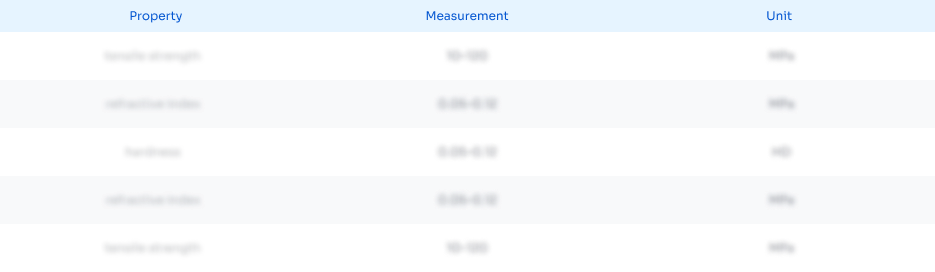
Abstract
Description
Claims
Application Information

- R&D
- Intellectual Property
- Life Sciences
- Materials
- Tech Scout
- Unparalleled Data Quality
- Higher Quality Content
- 60% Fewer Hallucinations
Browse by: Latest US Patents, China's latest patents, Technical Efficacy Thesaurus, Application Domain, Technology Topic, Popular Technical Reports.
© 2025 PatSnap. All rights reserved.Legal|Privacy policy|Modern Slavery Act Transparency Statement|Sitemap|About US| Contact US: help@patsnap.com