Preparation method of SiC/ZrO2 protective coating
A technology of protective coating and mass parts, applied in the field of preparation of SiC/ZrO2 protective coating, can solve the problems of high requirement of supercritical drying device, high production cost, low production efficiency, etc., so as to save sintering process and energy consumption cost. low, high productivity
- Summary
- Abstract
- Description
- Claims
- Application Information
AI Technical Summary
Problems solved by technology
Method used
Image
Examples
Embodiment 1
[0026] Such as figure 1 As shown, the present invention discloses a SiC / ZrO 2 The preparation method of protective coating comprises the following steps:
[0027] The first step, raw material premixing treatment, respectively weigh 35 parts by mass of micron-sized zirconia, 0.6 parts by mass of micron-sized molybdenum disulfide, 28 parts by mass of polycarbosilane precursor and 31.4 parts by mass of ethanol according to the mass fraction The solutions were put into vacuum ball mill jars respectively, and mixed evenly. The vacuum milling jar can be selected from an agate vacuum milling jar, a corundum vacuum milling jar, a zirconia vacuum milling jar or a cemented carbide vacuum milling jar as required;
[0028] The second step, vacuum ball milling treatment, vacuumize the vacuum ball milling tank after the raw material premixing treatment, add grinding balls, control the mass ratio of balls and materials to 9:1, and use planetary ball mill wet ball milling for 2 hours for co...
Embodiment 2
[0031] Such as figure 1 As shown, the present invention discloses a SiC / ZrO 2 The preparation method of protective coating comprises the following steps:
[0032] The first step, raw material premixing treatment, respectively weigh 55 parts by mass of micron-sized zirconia, 0.3 parts by mass of micron-sized molybdenum disulfide, 38 parts by mass of polycarbosilane precursor and 8.5 parts by mass of ethanol according to the mass fraction The solutions were put into vacuum ball mill jars respectively, and mixed evenly. The vacuum milling jar can be selected from an agate vacuum milling jar, a corundum vacuum milling jar, a zirconia vacuum milling jar or a cemented carbide vacuum milling jar as required;
[0033] The second step, vacuum ball milling treatment, vacuumize the vacuum ball milling tank after the raw material premixing treatment, add grinding balls, control the mass ratio of balls and materials to 5:1, and use planetary ball mill wet ball milling for 3 hours for conti...
Embodiment 3
[0036] Such as figure 1 As shown, the present invention discloses a SiC / ZrO 2 The preparation method of protective coating comprises the following steps:
[0037] The first step, raw material premixing treatment, respectively weigh 60 mass parts of micron-sized zirconia, 0.4 mass parts of micron-sized molybdenum disulfide, 25 mass parts of polycarbosilane precursor and 14.6 mass parts of ethanol according to mass fraction The solutions were put into vacuum ball mill jars respectively, and mixed evenly. The vacuum milling jar can be selected from an agate vacuum milling jar, a corundum vacuum milling jar, a zirconia vacuum milling jar or a cemented carbide vacuum milling jar as required;
[0038] The second step is vacuum ball milling. Vacuumize the vacuum ball mill tank after the raw material premixing process, add balls, control the mass ratio of balls and materials to 3:1, and use planetary ball mill wet ball milling for 4 hours for continuous reaction. In the process of...
PUM
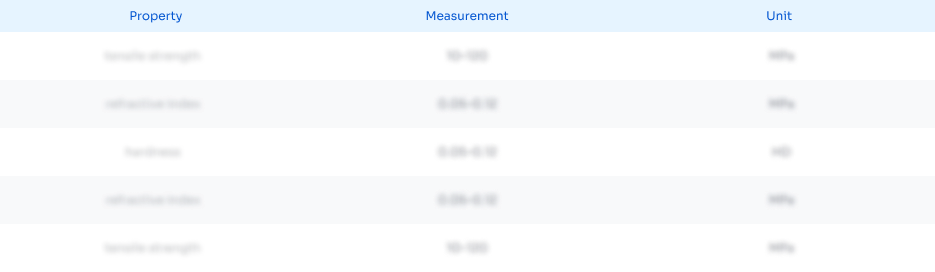
Abstract
Description
Claims
Application Information

- R&D Engineer
- R&D Manager
- IP Professional
- Industry Leading Data Capabilities
- Powerful AI technology
- Patent DNA Extraction
Browse by: Latest US Patents, China's latest patents, Technical Efficacy Thesaurus, Application Domain, Technology Topic, Popular Technical Reports.
© 2024 PatSnap. All rights reserved.Legal|Privacy policy|Modern Slavery Act Transparency Statement|Sitemap|About US| Contact US: help@patsnap.com