Superfine flexible fiber material and preparation method thereof
A fiber material and a flexible technology, applied in the field of ultra-fine denier flexible fiber material and preparation, to achieve the effect of improving flexibility, simple method, good hand feeling and heat resistance
- Summary
- Abstract
- Description
- Claims
- Application Information
AI Technical Summary
Problems solved by technology
Method used
Image
Examples
Embodiment 1
[0035] A method for preparing an ultrafine denier flexible fiber material, comprising:
[0036] 60 parts by weight of polyphenylene sulfide chips and 100 parts by weight of α-chloronaphthalene are uniformly mixed under the condition of 200 ° C to form the first mixed solution;
[0037] Add 2 parts by weight of pectin to 50 parts by weight of deionized water, stir and mix evenly to obtain a second mixed solution;
[0038] Mix 9 parts by weight of polylactic acid, 3 parts by weight of polytrimethylene carbonate, 3 parts by weight of polydioxanone and 3 parts by weight of polycaprolactone to obtain the first mixture;
[0039]Add the first mixed solution to the second mixed solution, stir and mix evenly, add the first mixture, 2 parts by weight of zinc oxide, 3 parts by weight of dilauryl thiopropionate and 2 parts by weight of polyethylene wax, stir and mix evenly to obtain spinning solution;
[0040] The spinning solution was spun with a spinning box to obtain an ultra-fine de...
Embodiment 2
[0042] A preparation method of an ultra-fine denier flexible fiber material, comprising:
[0043] 80 parts by weight of polyphenylene sulfide chips and 120 parts by weight of α-chloronaphthalene are mixed uniformly in the first mixed solution at 202°C;
[0044] Add 5 parts by weight of pectin to 80 parts by weight of deionized water, stir and mix to obtain a second mixed solution;
[0045] Mix 24 parts by weight of polylactic acid, 8 parts by weight of polytrimethylene carbonate, 8 parts by weight of polydioxanone and 8 parts by weight of polycaprolactone to obtain a first mixture;
[0046] Add the first mixed solution to the second mixed solution, stir and mix evenly, add the first mixture, 3.2 parts by weight of zinc oxide, 4.8 parts by weight of dilauryl thiopropionate and 5 parts by weight of polyethylene wax, stir and mix evenly to obtain spinning solution;
[0047] The spinning solution was spun with a spinning box to obtain an ultra-fine denier flexible fiber material...
Embodiment 3
[0049] A preparation method of an ultra-fine denier flexible fiber material, comprising:
[0050] A first mixed solution obtained by mixing 65 parts by weight of polyphenylene sulfide chips and 105 parts by weight of α-chloronaphthalene at a temperature of 204°C;
[0051] Add 3 parts by weight of pectin to 60 parts by weight of deionized water, stir and mix to obtain a second mixed solution;
[0052] Mix 12 parts by weight of polylactic acid, 4 parts by weight of polytrimethylene carbonate, 4 parts by weight of polydioxanone and 4 parts by weight of polycaprolactone to obtain a first mixture;
[0053] The first mixed solution was added into the second mixed solution, stirred and mixed evenly, and then 2.4 parts by weight of zinc oxide, 3.6 parts by weight of dilauryl thiopropionate and 3 parts by weight of polyethylene wax were added in the first mixture, and the mixture was stirred and mixed evenly to obtain a spinning solution. silk fluid;
[0054] The spinning solution wa...
PUM
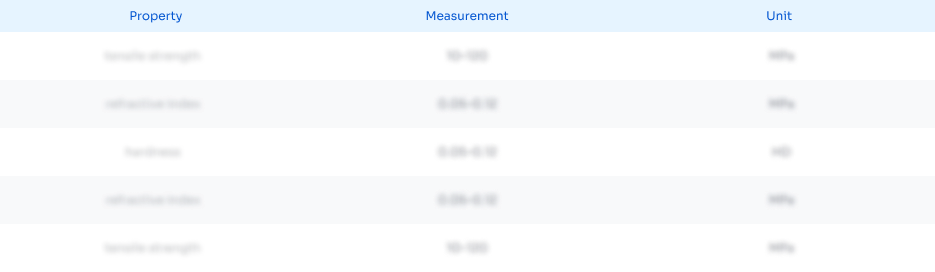
Abstract
Description
Claims
Application Information

- R&D
- Intellectual Property
- Life Sciences
- Materials
- Tech Scout
- Unparalleled Data Quality
- Higher Quality Content
- 60% Fewer Hallucinations
Browse by: Latest US Patents, China's latest patents, Technical Efficacy Thesaurus, Application Domain, Technology Topic, Popular Technical Reports.
© 2025 PatSnap. All rights reserved.Legal|Privacy policy|Modern Slavery Act Transparency Statement|Sitemap|About US| Contact US: help@patsnap.com