Method for cooling reduction crystallization of As2O3
An as2o3, crystallization technology, applied in the field of metallurgy, can solve the problems of adhesion and scaling, low efficiency of reduction crystallization, etc., and achieve the effects of reducing dosage, enhancing reduction effect, and reducing cleaning times
- Summary
- Abstract
- Description
- Claims
- Application Information
AI Technical Summary
Problems solved by technology
Method used
Image
Examples
Embodiment 1
[0034] As provided by the present invention 2 o 3 The cooling reduction system adopted in the cooling reduction crystallization method is composed of cooling tank one 11, cooling tank two 10, reaction tank one 9, reaction tank two 8 and transfer tank 7 connected in sequence. A water-cooling coil 12 is arranged in the cooling tank and the reaction tank. The cooling water is input in two ways, the first cooling water enters from the cooling water inlet pipe 1, first enters the water cooling coil 12 in the cooling tank two 10, then enters the water cooling coil 12 in the cooling tank one 11, and finally the cooling water comes out The water pipe 2 is output; the second cooling water enters from the cooling water inlet pipe 1, first enters the water cooling coil 12 in the reaction tank 2 8, then enters the water cooling coil 12 in the reaction tank 1 9, and finally flows through the cooling water outlet pipe 2 output. This setup can avoid the As 2 o 3 The phenomenon of rapid ...
Embodiment 2
[0037] (1) Send 200L of arsenic-containing high-temperature leachate into cooling tank 1 provided with a water-cooling coil, and pass cold water into the water-cooling coil for primary cooling.
[0038] The primary cooled liquid is sent to the second cooling tank provided with a water-cooled coil, and cold water is passed into the water-cooled coil for secondary cooling until the liquid temperature is 38°C.
[0039] (2) Place the cooled liquid in reaction tank one, feed sulfur dioxide gas therein, reduce for 2 hours, stop feeding sulfur dioxide gas, input reaction tank two, and let it stand for 3 hours. While feeding the sulfur dioxide gas, the cold water input into the water-cooled coils in the reaction tank 1 and the reaction tank 2 is cooled. Calculated according to the molar ratio, arsenic in the liquid: sulfur dioxide = 2. The gas after reduction treatment is collected and washed with lye before being discharged.
[0040] The cold water in the step (1) and the step (2) ...
Embodiment 3
[0044] (1) Send 500L of arsenic-containing high-temperature leaching solution into cooling tank 1 provided with a water-cooling coil, and pass cold water into the water-cooling coil for primary cooling.
[0045] The primary cooled liquid is sent to the second cooling tank provided with a water-cooled coil, and cold water is passed into the water-cooled coil for secondary cooling until the liquid temperature is 36°C.
[0046](3) Place the cooled liquid in reaction tank one, feed sulfur dioxide gas therein, reduce for 2.5 hours, stop feeding sulfur dioxide gas, enter reaction tank two, and let it stand for 3.5 hours. While feeding the sulfur dioxide gas, the cold water input into the water-cooled coils in the reaction tank 1 and the reaction tank 2 is cooled. Calculated according to the molar ratio, arsenic in the liquid: sulfur dioxide = 2.5. The gas after reduction treatment is collected and washed with lye before being discharged.
[0047] The cold water in the step (1) and...
PUM
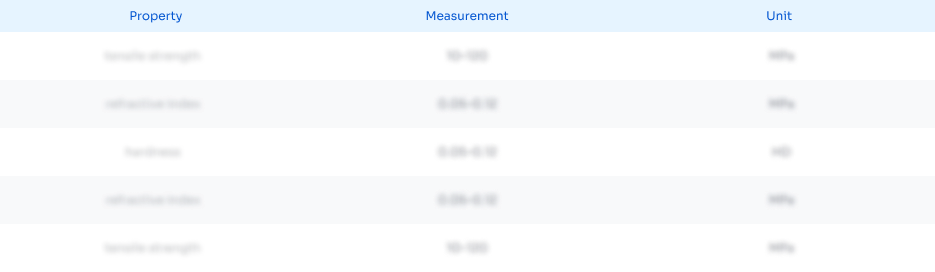
Abstract
Description
Claims
Application Information

- R&D
- Intellectual Property
- Life Sciences
- Materials
- Tech Scout
- Unparalleled Data Quality
- Higher Quality Content
- 60% Fewer Hallucinations
Browse by: Latest US Patents, China's latest patents, Technical Efficacy Thesaurus, Application Domain, Technology Topic, Popular Technical Reports.
© 2025 PatSnap. All rights reserved.Legal|Privacy policy|Modern Slavery Act Transparency Statement|Sitemap|About US| Contact US: help@patsnap.com