Extrusion grade polypropylene material with high heat resistance and method for preparing extrusion grade polypropylene material
A polypropylene material, high heat-resistant technology, applied in the field of polypropylene materials, can solve the problems of poor impact strength, aging resistance and heat resistance, achieve excellent heat resistance, long oxidation induction time, reduce catalytic induction The effect of action
- Summary
- Abstract
- Description
- Claims
- Application Information
AI Technical Summary
Problems solved by technology
Method used
Image
Examples
Embodiment 1
[0030] Put 46g PPR1042, 30g talcum powder AH51210, 19g toughening agent-8150, 1g compound heat-resistant agent, 0.3g EBS / P-130, 0.2g antioxidant 1010 and 0.4g antioxidant 168 into the high-speed After mixing in the mixer for 5-8 minutes, take it out, carry out melt blending extrusion, traction, and granulation in a twin-screw extruder, the temperature of the barrel of the extruder is 170-195 ° C, and the main screw speed is fixed at 180 rpm. The obtained pellets were injection-molded using an injection molding machine at an injection molding temperature of 190° C. to obtain ISO standard mechanical test specimens for product performance testing. See Table 1 for test data.
Embodiment 2
[0032] Put 80g PPK8003, 10g talcum powder AH51210, 3g toughening agent-8150, 0.4g compound heat-resistant agent, 0.5g EBS / P-130, 0.1g antioxidant 1010 and 0.2g antioxidant 168 into the above ratio Take it out after mixing in the high-speed mixer for 5-8 minutes, and carry out melt blending, extrusion, traction, and granulation in the twin-screw extruder. . The obtained pellets were injection-molded using an injection molding machine at an injection molding temperature of 190° C. to obtain ISO standard mechanical test specimens for product performance testing. See Table 1 for test data.
Embodiment 3
[0034] Put 65g PPK8303, 20g talcum powder AH51210, 14g toughening agent-8842, 1g compound heat-resistant agent, 0.1g EBS / P-130, 0.3g antioxidant 1010 and 0.3g antioxidant 168 into the high-speed After mixing in the mixer for 5-8 minutes, take it out, carry out melt blending extrusion, traction, and granulation in a twin-screw extruder, the temperature of the barrel of the extruder is 170-195 ° C, and the main screw speed is fixed at 180 rpm. The obtained pellets were injection-molded using an injection molding machine at an injection molding temperature of 190° C. to obtain ISO standard mechanical test specimens for product performance testing. See Table 1 for test data.
PUM
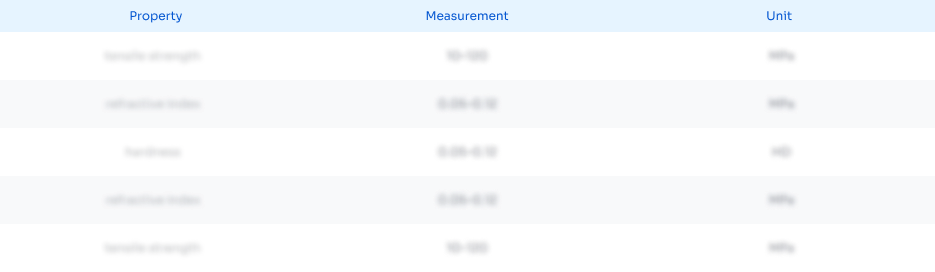
Abstract
Description
Claims
Application Information

- R&D Engineer
- R&D Manager
- IP Professional
- Industry Leading Data Capabilities
- Powerful AI technology
- Patent DNA Extraction
Browse by: Latest US Patents, China's latest patents, Technical Efficacy Thesaurus, Application Domain, Technology Topic, Popular Technical Reports.
© 2024 PatSnap. All rights reserved.Legal|Privacy policy|Modern Slavery Act Transparency Statement|Sitemap|About US| Contact US: help@patsnap.com