High-strength magnetic core and preparation method thereof
A high-strength, magnetic core technology, applied in the direction of inorganic material magnetism, can solve the problems of unreasonable production process of magnetic core, short service life of magnetic core, low strength of magnetic core, etc., achieve superior performance, prolong service life and increase strength Effect
- Summary
- Abstract
- Description
- Claims
- Application Information
AI Technical Summary
Problems solved by technology
Method used
Examples
Embodiment 1
[0024] A high-strength magnetic core, the magnetic core is made of the following raw materials in parts by weight: 50 parts of iron oxide, 18 parts of copper oxide, 12 parts of zinc oxide, 6 parts of nickel oxide, 14 parts of dichromium trioxide, 12 parts of nickel carbonate 10 parts of manganese carbonate, 8 parts of cobalt oxide, 6 parts of magnesium hydroxide, 14 parts of trimanganese tetraoxide, 12 parts of chromium carbide, 10 parts of tungsten carbide, 8 parts of polonium oxide, 6 parts of aluminum hydroxide, coupling agent 2 1 part, 1 part of accelerator, 1 part of defoamer.
[0025] Wherein, the coupling agent is formed by mixing a silane coupling agent, a titanate coupling agent and a zirconium coupling agent in a mass ratio of 3:2:4; the accelerator is composed of dibutyltin dilaurate, dibutyltin Methylaminomethylphenol and triethanolamine are mixed in a mass ratio of 4:3:1; the defoamer is composed of emulsified silicone oil, polyoxyethylene polyoxypropanolamine eth...
Embodiment 2
[0033] A high-strength magnetic core, the magnetic core is made of the following raw materials in parts by weight: 52 parts of iron oxide, 20 parts of copper oxide, 14 parts of zinc oxide, 8 parts of nickel oxide, 16 parts of dichromium trioxide, 14 parts of nickel carbonate 12 parts of manganese carbonate, 10 parts of cobalt oxide, 8 parts of magnesium hydroxide, 16 parts of trimanganese tetraoxide, 14 parts of chromium carbide, 12 parts of tungsten carbide, 10 parts of polonium oxide, 8 parts of aluminum hydroxide, 3 parts of coupling agent 2 parts, accelerator 2 parts, defoamer 2 parts.
[0034] Wherein, the coupling agent is formed by mixing a silane coupling agent, a titanate coupling agent and a zirconium coupling agent in a mass ratio of 3:2:4; the accelerator is composed of dibutyltin dilaurate, dibutyltin Methylaminomethylphenol and triethanolamine are mixed in a mass ratio of 4:3:1; the defoamer is composed of emulsified silicone oil, polyoxyethylene polyoxypropanola...
Embodiment 3
[0042] A high-strength magnetic core, the magnetic core is made of the following raw materials in parts by weight: 54 parts of iron oxide, 22 parts of copper oxide, 6 parts of zinc oxide, 10 parts of nickel oxide, 18 parts of dichromium trioxide, 16 parts of nickel carbonate 14 parts, manganese carbonate 14 parts, cobalt oxide 12 parts, magnesium hydroxide 10 parts, trimanganese tetraoxide 18 parts, chromium carbide 16 parts, tungsten carbide 14 parts, polonium oxide 12 parts, aluminum hydroxide 10 parts, coupling agent 4 3 parts, accelerator 3 parts, defoamer 3 parts.
[0043] Wherein, the coupling agent is formed by mixing a silane coupling agent, a titanate coupling agent and a zirconium coupling agent in a mass ratio of 3:2:4; the accelerator is composed of dibutyltin dilaurate, dibutyltin Methylaminomethylphenol and triethanolamine are mixed in a mass ratio of 4:3:1; the defoamer is composed of emulsified silicone oil, polyoxyethylene polyoxypropanolamine ether and polydi...
PUM
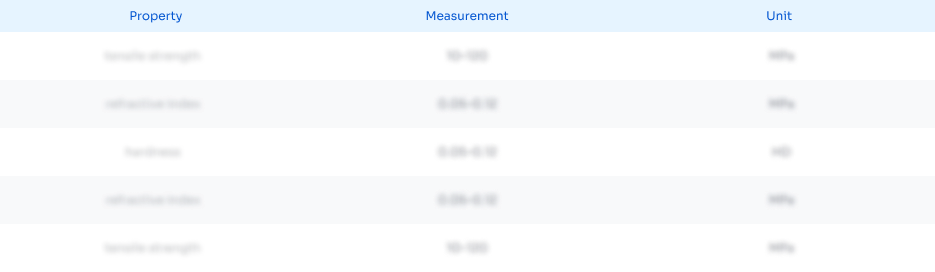
Abstract
Description
Claims
Application Information

- Generate Ideas
- Intellectual Property
- Life Sciences
- Materials
- Tech Scout
- Unparalleled Data Quality
- Higher Quality Content
- 60% Fewer Hallucinations
Browse by: Latest US Patents, China's latest patents, Technical Efficacy Thesaurus, Application Domain, Technology Topic, Popular Technical Reports.
© 2025 PatSnap. All rights reserved.Legal|Privacy policy|Modern Slavery Act Transparency Statement|Sitemap|About US| Contact US: help@patsnap.com