Process for combined production of polyferric sulfate and ferric trichloride by two-step acid dissolution method of fine iron powder
A technology for polymerizing ferric sulfate and ferric chloride, which is applied in the direction of ferric sulfate and ferric halide, can solve the problem of no joint production of polymeric ferric sulfate and ferric chloride, and achieve the effect of broadening the production process and reducing production costs
- Summary
- Abstract
- Description
- Claims
- Application Information
AI Technical Summary
Problems solved by technology
Method used
Image
Examples
Embodiment 1
[0035] Such as figure 1 As shown, the co-production of polyferric sulfate and ferric chloride by the two-step acid-dissolving method of iron fine powder comprises the following steps:
[0036] 1) Add iron concentrate powder into dilute sulfuric acid for leaching to obtain the first step of acid solution; iron concentrate powder is hematite powder after magnetic separation, its particle size is 100-200 mesh, and the total iron content is above 50%. The step is carried out in an acid-resistant reaction kettle, the mass concentration of the dilute sulfuric acid is 25%, the mass ratio of the total iron in the iron concentrate powder to the sulfuric acid in the dilute sulfuric acid is 1:2.0; the leaching conditions include: the pressure is normal pressure, the temperature is 110°C, leaching time is 1.5 hours;
[0037] 2) Use magnesite powder to adjust the acidity of the acid solution in the first step; this adjustment step is completed in the acid-resistant adjustment tank, mainly...
Embodiment 2
[0045] Such as figure 1 As shown, the co-production of polyferric sulfate and ferric chloride by the two-step acid-dissolving method of iron fine powder comprises the following steps:
[0046] 1) Add iron concentrate powder into dilute sulfuric acid for leaching to obtain the first step acid solution; iron concentrate powder is pyrite slag without magnetic separation, its particle size is 100-200 mesh, and the total iron content is above 50% , the leaching step is carried out in an acid-resistant reactor, the mass concentration of the dilute sulfuric acid is 35%, the mass ratio of the total iron in the iron concentrate powder to the sulfuric acid in the dilute sulfuric acid is 1:2.5; the leaching conditions include: the pressure is 1kgf / cm² , the temperature is 120°C, and the leaching time is 1.5 hours;
[0047] 2) Use ferrous sulfate solid to adjust the acidity of the first step acid solution; this adjustment step is completed in the acid-resistant adjustment tank, mainly to...
Embodiment 3
[0055] Such as figure 1 As shown, the co-production of polyferric sulfate and ferric chloride by the two-step acid-dissolving method of iron fine powder comprises the following steps:
[0056] 1) Add iron concentrate powder into dilute sulfuric acid for leaching to obtain the first step of acid solution; iron concentrate powder is magnetite powder after magnetic separation, its particle size is 100-200 mesh, and the total iron content is above 50%. The steps are carried out in an acid-resistant reaction kettle, the mass concentration of the dilute sulfuric acid is 45%, the mass ratio of the total iron in the iron concentrate powder to the sulfuric acid in the dilute sulfuric acid is 1:3.0; the leaching conditions include: the pressure is 1.5kgf / cm², The temperature is 110°C, and the leaching time is 1.8 hours;
[0057] 2) Use magnesite powder to adjust the acidity of the acid solution in the first step; this adjustment step is completed in the acid-resistant adjustment tank, ...
PUM
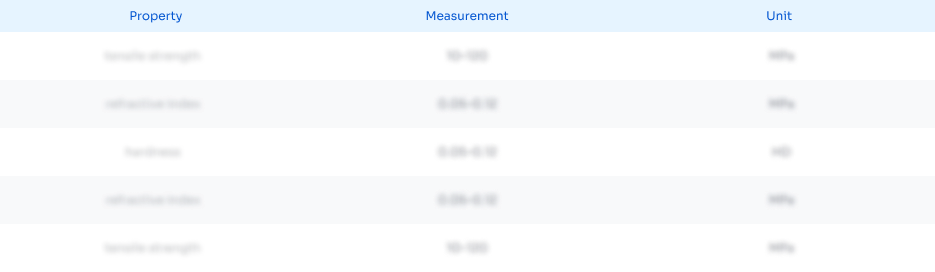
Abstract
Description
Claims
Application Information

- R&D
- Intellectual Property
- Life Sciences
- Materials
- Tech Scout
- Unparalleled Data Quality
- Higher Quality Content
- 60% Fewer Hallucinations
Browse by: Latest US Patents, China's latest patents, Technical Efficacy Thesaurus, Application Domain, Technology Topic, Popular Technical Reports.
© 2025 PatSnap. All rights reserved.Legal|Privacy policy|Modern Slavery Act Transparency Statement|Sitemap|About US| Contact US: help@patsnap.com