Stationary shaft shoulder friction stir welding method capable of coaxially adding materials by forming groove
A technology of friction stir welding and static shoulder, which is applied in the field of welding and static shoulder friction stir welding, can solve the problems of stress concentration, joint flash, weld thinning, etc., and achieve a wide range of applicable materials and improve applicability , to avoid the effect of metal inclusions
- Summary
- Abstract
- Description
- Claims
- Application Information
AI Technical Summary
Problems solved by technology
Method used
Image
Examples
Embodiment
[0021] The present invention will be described in more detail below with reference to the accompanying drawings. These examples are only descriptions of the best embodiments of the present invention, and do not limit the scope of the present invention in any way. The present invention will be further described in detail below in conjunction with the accompanying drawings and specific embodiments.
specific Embodiment approach 1
[0022] Specific implementation mode one: the following combination figure 1 , figure 2 , image 3 To describe this embodiment, figure 1 Shown is a schematic diagram of static shoulder friction stir welding of flat butt grooved coaxial filling materials. A U-shaped groove 12 is made on the base metal to be welded. The stirring tool is composed of a rotating stirring pin 6 and a stationary shoulder 8. The static shoulder 8 is fixed on the main shaft base 5, the stirring pin 6 is composed of the same material as the base metal 10 to be welded, and the end of the stirring pin is processed into a shape slightly smaller than the U-shaped groove 12 section size. During welding, the stirring pin 6 rotates at a high speed at a speed ω, and at the same time exerts an axial force on the stirring pin 6 and maintains a downward feed speed b. When the stirring pin 6 contacts the base material 10 to be welded, friction heat generation begins, and the friction area on the contact surface ...
PUM
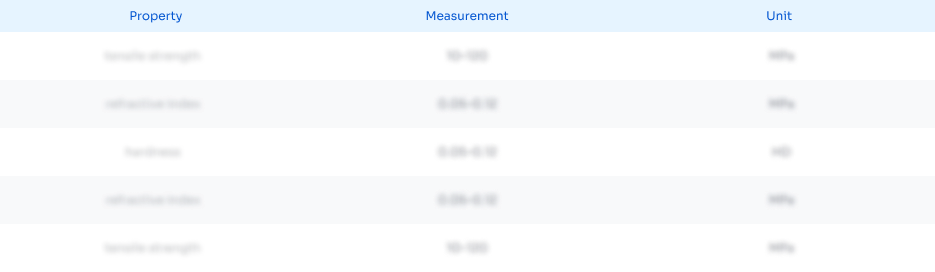
Abstract
Description
Claims
Application Information

- R&D
- Intellectual Property
- Life Sciences
- Materials
- Tech Scout
- Unparalleled Data Quality
- Higher Quality Content
- 60% Fewer Hallucinations
Browse by: Latest US Patents, China's latest patents, Technical Efficacy Thesaurus, Application Domain, Technology Topic, Popular Technical Reports.
© 2025 PatSnap. All rights reserved.Legal|Privacy policy|Modern Slavery Act Transparency Statement|Sitemap|About US| Contact US: help@patsnap.com