A method for integrally manufacturing trash rack panels in drainage chambers
A technology of overall production and drainage chambers, which is applied in water conservancy projects, hydroelectric power generation, hydroelectric power stations, etc., and can solve the problems of poor product quality, difficult to reach, and long production cycle.
- Summary
- Abstract
- Description
- Claims
- Application Information
AI Technical Summary
Problems solved by technology
Method used
Image
Examples
Embodiment 1
[0029] A method for integrally manufacturing a trash rack plate in a drainage chamber, comprising the following steps:
[0030] (1) Measurement and material selection
[0031] Measuring the size of the water outlet of the drainage chamber, selecting tiles, the top and bottom of the tiles have an arc structure, and the size of the tiles is larger than the size of the water outlet of the drainage chamber;
[0032] (2) Determine the opening position
[0033] According to the outlet size of the drainage chamber measured in step (1), determine the reserved position of the trash rack plate on the tile, and the reserved position shall not be at the edge of the tile;
[0034] (3) cutting
[0035] Cut the tile according to the reserved position determined in step (2), and reserve a hole, and leave at least 2 breakpoints on the edge to be bent in the reserved hole during rolling;
[0036] (4) Install the trash rack plate
[0037] Install the trash rack plate into the reserved hole c...
PUM
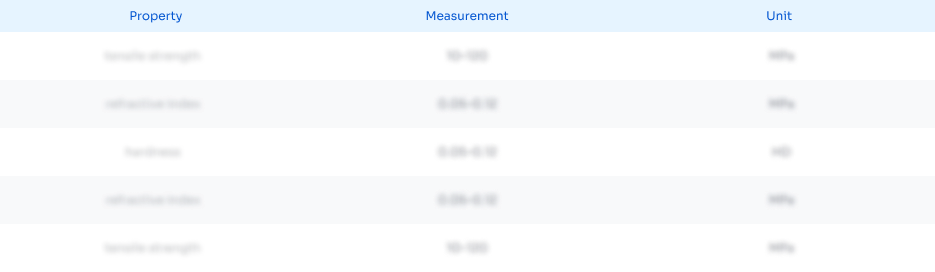
Abstract
Description
Claims
Application Information

- R&D
- Intellectual Property
- Life Sciences
- Materials
- Tech Scout
- Unparalleled Data Quality
- Higher Quality Content
- 60% Fewer Hallucinations
Browse by: Latest US Patents, China's latest patents, Technical Efficacy Thesaurus, Application Domain, Technology Topic, Popular Technical Reports.
© 2025 PatSnap. All rights reserved.Legal|Privacy policy|Modern Slavery Act Transparency Statement|Sitemap|About US| Contact US: help@patsnap.com