An ultrasonic-assisted multi-beam laser fuse additive manufacturing equipment and method
An additive manufacturing and ultrasonic-assisted technology, which is applied in the field of additive manufacturing, can solve problems such as difficult control of the forming quality of laser fuse additives, restrictions on the development of laser fuse additive technology, and reduced sensitivity of the camera system, so as to reduce the overall Effect of heat input, reduction of deformation, and improvement of mechanical properties
- Summary
- Abstract
- Description
- Claims
- Application Information
AI Technical Summary
Problems solved by technology
Method used
Image
Examples
Embodiment Construction
[0042] In order to make the object, technical solution and advantages of the present invention clearer, the present invention will be further described in detail below in conjunction with the accompanying drawings and embodiments. It should be understood that the specific embodiments described here are only used to explain the present invention, not to limit the present invention. In addition, the technical features involved in the various embodiments of the present invention described below can be combined with each other as long as they do not constitute a conflict with each other.
[0043] Such as Figure 1 to Figure 4 As shown, an ultrasonic-assisted multi-beam laser fuse additive manufacturing equipment is characterized in that it includes a laser device, a wire feeding mechanism 3, a substrate 10, a wire guide head 9, an electromagnetic ultrasonic generator 4, and an electromagnetic ultrasonic probe 13 , a controller and a protective gas protection box 21, wherein,
[...
PUM
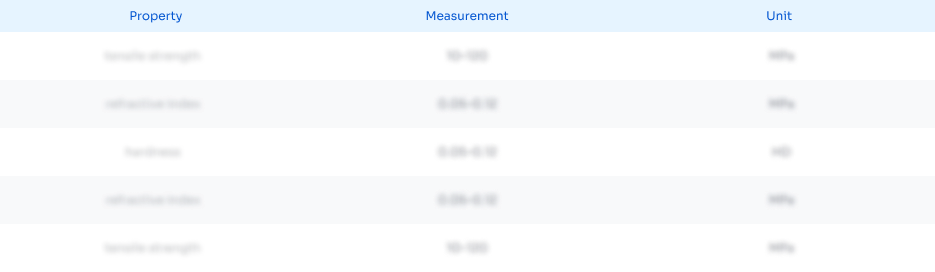
Abstract
Description
Claims
Application Information

- R&D
- Intellectual Property
- Life Sciences
- Materials
- Tech Scout
- Unparalleled Data Quality
- Higher Quality Content
- 60% Fewer Hallucinations
Browse by: Latest US Patents, China's latest patents, Technical Efficacy Thesaurus, Application Domain, Technology Topic, Popular Technical Reports.
© 2025 PatSnap. All rights reserved.Legal|Privacy policy|Modern Slavery Act Transparency Statement|Sitemap|About US| Contact US: help@patsnap.com