Electrochemical reduction-thermochemical cycle water-splitting hydrogen production method
A thermochemical cycle and electrochemical technology, applied in chemical instruments and methods, inorganic chemistry, hydrogen production, etc., can solve problems such as high temperature and difficult matching of heat sources, and achieve easy implementation, avoid material problems, eliminate heat loss and time wasting effect
- Summary
- Abstract
- Description
- Claims
- Application Information
AI Technical Summary
Problems solved by technology
Method used
Image
Examples
Embodiment 1
[0028] Embodiment 1: Electrochemical reduction generates iron.
[0029] Step 1: Weigh 23.55g of 56.5mol% Li 0.87 Na 0.63 K 0.50 CO 3 – 43.5mol% LiOH mixture, and then weighed 1.87 g of Fe 2 o 3 Grind and mix well, use a nickel sheet as the anode (1 cm × 3 cm), and a 304 stainless steel sheet (1 cm × 3 cm) as the cathode, fix the anode and cathode, and put the ground and mixed electrolyte into a corundum crucible.
[0030] Step 2: Put the corundum crucible into an electric furnace to heat up to 500°C, and connect the anode and cathode to a DC power supply.
[0031] Step 3: Turn on the power supply and perform constant current electrolysis at 0.5 A for 240 min.
[0032] Step 4: After the electrolysis, cut off the power supply, take out the cathode, and use XRD to analyze the electrolysis product on the electrolyte and the cathode. The results are shown in figure 1 ,Depend on figure 1 It can be seen that iron is generated on the cathode after electrolysis.
Embodiment 2
[0034] Step 1 and Step 2 of this embodiment are the same as Step 1 and Step 2 in Embodiment 1.
[0035] Step 3: Turn on the power, and electrolyze for 5, 10, 20, 40 and 60 min at a constant current of 0.5 A, respectively.
[0036] Step 4: Cut off the power supply after the electrolysis, and then use the N with a flow rate of 80 mL / min 2 Water vapor at 250°C was carried and blown to the stainless steel sheet cathode to react with the new ecological Fe formed by electrolysis for 120 min.
[0037] Step 5: The gas discharged from the electrolytic cell is collected by the drainage and gas collection method, and the hydrogen content is analyzed by gas chromatography. see results figure 2 , it can be seen from the figure that as the electrolysis time increases, the amount of hydrogen produced increases, and the current efficiencies at 5, 10, 20, 40 and 60 min are 13.3%, 28.9%, 21.5%, 23.1% and 27.1% respectively .
Embodiment 3
[0039] Step 1 and Step 2 of this embodiment are the same as Step 1 and Step 2 in Embodiment 1.
[0040] Step 3: Turn on the power, and electrolyze for 60 min at a constant current of 0.5 A.
[0041] Step 4 of this embodiment is the same as step 4 in specific embodiment 2.
[0042] Step 5: The gas discharged from the electrolytic cell is collected by the drainage and gas collection method, and the hydrogen content is analyzed by gas chromatography.
[0043] Step 6: Recycle back to Step 1 of this embodiment to carry out the next electrochemical reduction process - thermochemical water splitting process to produce hydrogen. see results image 3 , it can be seen from the figure that the hydrogen production and current efficiency of the electrochemical reduction process-thermochemical water splitting process for hydrogen production are basically constant for 4 cycles, indicating that the electrochemical reduction process-thermochemical water splitting process for hydrogen productio...
PUM
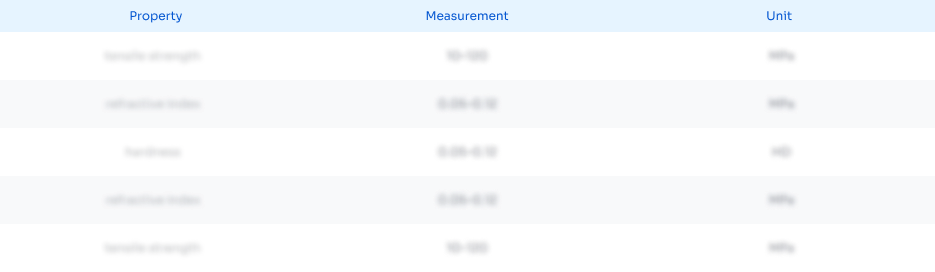
Abstract
Description
Claims
Application Information

- R&D
- Intellectual Property
- Life Sciences
- Materials
- Tech Scout
- Unparalleled Data Quality
- Higher Quality Content
- 60% Fewer Hallucinations
Browse by: Latest US Patents, China's latest patents, Technical Efficacy Thesaurus, Application Domain, Technology Topic, Popular Technical Reports.
© 2025 PatSnap. All rights reserved.Legal|Privacy policy|Modern Slavery Act Transparency Statement|Sitemap|About US| Contact US: help@patsnap.com