Modified polyformaldehyde material
A polyoxymethylene material and technology of polyoxymethylene, applied in the field of modified polyoxymethylene material and its preparation, can solve problems such as not easy to absorb moisture, achieve the effect of improving shrinkage performance and safety performance
- Summary
- Abstract
- Description
- Claims
- Application Information
AI Technical Summary
Problems solved by technology
Method used
Image
Examples
Embodiment 1
[0021] (1) Weigh each raw material according to the weight ratio as follows:
[0022] POM raw material: 75
[0023] E-glass fiber: 25
[0024] Antioxidant (ethylene-octene copolymer): 2.0
[0025] Colorant: 0.8
[0026] UV absorber (2-hydroxy-4-n-octyloxybenzophenone): 9.0
[0027] Light stabilizer: 9.0
[0028] Dispersed lubricant (TAS-2A): 1.0
[0029] Glass fiber compatibilizer: 5.0
[0030] (2) First dry mix the above-mentioned various raw materials in a high-speed mixer for 3-5 minutes, and then put them in a twin-screw extruder to melt and extrude, cool, pelletize, and pack the finished product; among them, the twin-screw extruder The temperature of the first zone is 90-100°C, the second zone is 150-180°C, the third zone is 200-210°C, the fourth zone is 200-205°C; the fifth zone is 190-200°C, and the residence time is 1-2 minutes , the pressure is 10-15Mpa.
[0031] Experimental results:
[0032] Characteristic parameters
[0033] The above experimenta...
Embodiment 2
[0035] (1) Weigh each raw material according to the weight ratio as follows:
[0036] POM raw material: 70
[0037] E-glass fiber: 20
[0038] Antioxidant (ethylene-octene copolymer): 1.8
[0039] Colorant: 0.6
[0040] UV absorber (2-hydroxy-4-n-octyloxybenzophenone): 8.5
[0041] Light stabilizer: 8.5
[0042] Dispersed lubricant (TAS-2A): 0.8 Glass fiber compatibilizer: 4.5
[0043] (2) First dry mix the above-mentioned various raw materials in a high-speed mixer for 3-5 minutes, and then put them in a twin-screw extruder to melt and extrude, cool, pelletize, and pack the finished product; among them, the twin-screw extruder The temperature of the first zone is 90-100°C, the second zone is 150-180°C, the third zone is 200-210°C, the fourth zone is 200-205°C; the fifth zone is 190-200°C, and the residence time is 1-2 minutes , the pressure is 10-15Mpa.
[0044] Experimental results:
[0045] Characteristic parameters
[0046] The above test results show tha...
Embodiment 3
[0048] (1) Weigh each raw material according to the weight ratio as follows:
[0049] POM raw material: 80
[0050] E-glass fiber: 30
[0051] Antioxidant (ethylene-octene copolymer): 2.2
[0052] Colorant: 1.0
[0053] UV absorber (2-hydroxy-4-n-octyloxybenzophenone): 9.5
[0054] Light stabilizer: 9.5
[0055] Dispersed lubricant (TAS-2A): 1.2
[0056] Glass fiber compatibilizer: 5.5
[0057] (2) First dry mix the above-mentioned various raw materials in a high-speed mixer for 3-5 minutes, and then put them in a twin-screw extruder to melt and extrude, cool, pelletize, and pack the finished product; among them, the twin-screw extruder The temperature of the first zone is 90-100°C, the second zone is 150-180°C, the third zone is 200-210°C, the fourth zone is 200-205°C; the fifth zone is 190-200°C, and the residence time is 1-2 minutes , the pressure is 10-15Mpa.
[0058] Experimental results:
[0059] Characteristic parameters
Performan...
PUM
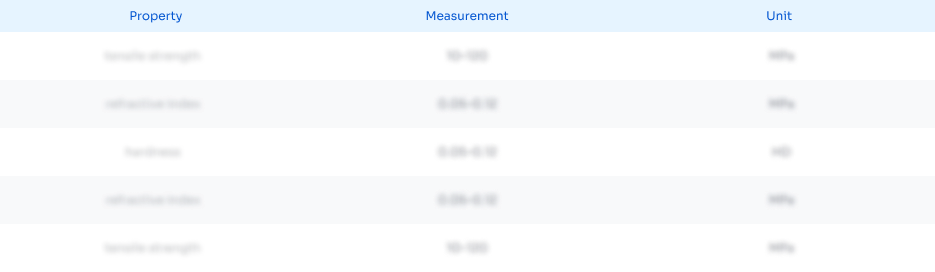
Abstract
Description
Claims
Application Information

- R&D
- Intellectual Property
- Life Sciences
- Materials
- Tech Scout
- Unparalleled Data Quality
- Higher Quality Content
- 60% Fewer Hallucinations
Browse by: Latest US Patents, China's latest patents, Technical Efficacy Thesaurus, Application Domain, Technology Topic, Popular Technical Reports.
© 2025 PatSnap. All rights reserved.Legal|Privacy policy|Modern Slavery Act Transparency Statement|Sitemap|About US| Contact US: help@patsnap.com