Non-isocyanate waterborne polyurea and preparation method thereof
A non-isocyanate, polyurea technology, applied in the polymer field, can solve the problems of polyurea infiltration and high construction requirements, and achieve the effects of improving mechanical properties, improving adhesion and prolonging gel time.
- Summary
- Abstract
- Description
- Claims
- Application Information
AI Technical Summary
Problems solved by technology
Method used
Image
Examples
Embodiment 1
[0021] A non-isocyanate water-based polyurea, containing the following components in parts by mass: 1,6-hexanediamine, 5.5 parts; dimethyl carbonate, 34 parts; sodium methoxide, 0.05 parts; diethylenetriamine, 1.2 parts; Acid tetrabutyl ester, 0.05 part; Amino-terminated polyether D230, 15 parts; Glacial acetic acid, 0.7 part; Deionized water, 45 parts; Concrete preparation steps are as follows:
[0022] (1) Weigh 1,6-hexamethylenediamine, sodium methoxide and dimethyl carbonate according to the above-mentioned mass fractions, first add dimethyl carbonate, start stirring, raise the temperature to 40~60°C, and start slowly dripping Add hexamethylenediamine, after the dropwise addition, raise the temperature to 70~100°C, remove methanol, and obtain a carbonate-terminated methyl carbamate oligomer after a reaction time of 8~24 hours;
[0023] (2) Add the hydrophilic chain extender diethylenetriamine dropwise to the carbonate-terminated methyl carbamate oligomer in the above prepa...
Embodiment 2
[0029] A non-isocyanate water-based polyurea, containing the following components in parts by mass: 1,4-butanediamine, 6.5 parts; dimethyl carbonate, 22 parts; sodium methoxide, 0.05 parts; diethylenetriamine, 1.4 parts; titanium Acid tetrabutyl ester, 0.05 part; Amino-terminated polyether D400, 18 parts; Glacial acetic acid, 0.8 part; Deionized water, 54 parts; Concrete preparation steps are as follows:
[0030] (1) Weigh 1,4-butylene diamine, sodium methoxide and dimethyl carbonate according to the above mass fractions, first add dimethyl carbonate, start stirring, raise the temperature to 40~60°C, and start slowly dripping Add 1,4-butanediamine, and after the dropwise addition, raise the temperature to 70~100°C to remove methanol, and obtain a carbonate-terminated methyl carbamate oligomer after a reaction time of 8~24 hours;
[0031] (2) Add the hydrophilic chain extender diethylenetriamine dropwise to the carbonate-terminated methyl carbamate oligomer in the above prepara...
Embodiment 3
[0037] A non-isocyanate water-based polyurea, containing the following components in parts by mass: 1,4-butanediamine, 7 parts; dimethyl carbonate, 30 parts; sodium methoxide, 0.05 parts; diethylenetriamine, 1.5 parts; titanium Acid tetrabutyl ester, 0.05 part; Amino-terminated polyether D230, 20 parts; Glacial acetic acid, 0.8 part; Deionized water, 54 parts; Concrete preparation steps are as follows:
[0038] (1) Weigh 1,4-butylene diamine, sodium methoxide and dimethyl carbonate according to the above mass fractions, first add dimethyl carbonate, start stirring, raise the temperature to 40~60°C, and start slowly dripping Add 1,4-butanediamine, and after the dropwise addition, raise the temperature to 70~100°C to remove methanol, and obtain a carbonate-terminated methyl carbamate oligomer after a reaction time of 8~24 hours;
[0039] (2) Add the hydrophilic chain extender diethylenetriamine dropwise to the carbonate-terminated methyl carbamate oligomer in the above preparati...
PUM
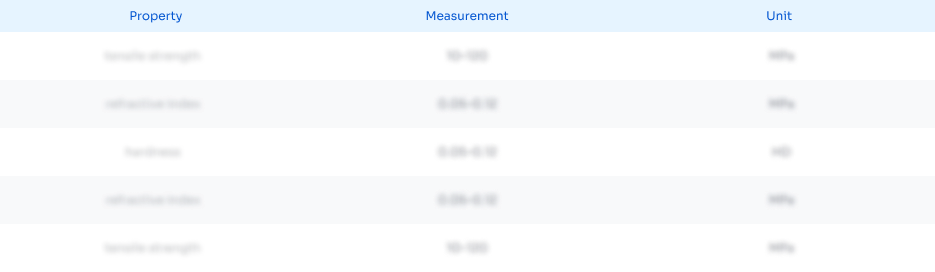
Abstract
Description
Claims
Application Information

- R&D
- Intellectual Property
- Life Sciences
- Materials
- Tech Scout
- Unparalleled Data Quality
- Higher Quality Content
- 60% Fewer Hallucinations
Browse by: Latest US Patents, China's latest patents, Technical Efficacy Thesaurus, Application Domain, Technology Topic, Popular Technical Reports.
© 2025 PatSnap. All rights reserved.Legal|Privacy policy|Modern Slavery Act Transparency Statement|Sitemap|About US| Contact US: help@patsnap.com