Prefabricated box beam steel bar framework bundling hydraulic formwork and construction method
A technology of steel skeleton and hydraulic mold, applied in manufacturing tools, ceramic molding machines, building structures, etc., can solve the problems of high labor intensity of operators, difficulty of U-shaped steel skeleton, affecting the accuracy of U-shaped steel skeleton, etc.
- Summary
- Abstract
- Description
- Claims
- Application Information
AI Technical Summary
Problems solved by technology
Method used
Image
Examples
Embodiment Construction
[0074] The embodiments of the present invention will be described in detail below according to the above-mentioned drawings.
[0075] Such as Figure 1~Figure 3 As shown, 1. Track, 2. Fixed base, 21. Longitudinal beam, 211. Longitudinal beam square steel, 212. Longitudinal beam channel steel, 22. Cross beam, 23. Longitudinal beam positioning slot, 24. Cross beam positioning slot, 3. Mobile frame , 31. Vertical frame, 32. Underframe, 33. Top corrugation, 34. Secondary rib positioning rod, 35. Vertical stirrup positioning rod, 36. Vertical stirrup positioning groove, 37. Bracket, 4. Moving wheel, 41 . Moving wheel A, 42. Moving wheel B, 5. Hydraulic system, 51. Hydraulic rod, 6. Steel frame, 61. Main reinforcement, 62. Secondary reinforcement, 63. Flat stirrup, 64. Vertical stirrup.
[0076] A hydraulic formwork and construction method for binding prefabricated box girder reinforcing steel frame, such as figure 1 As shown, it mainly relates to the field of bridge construction.
[007...
PUM
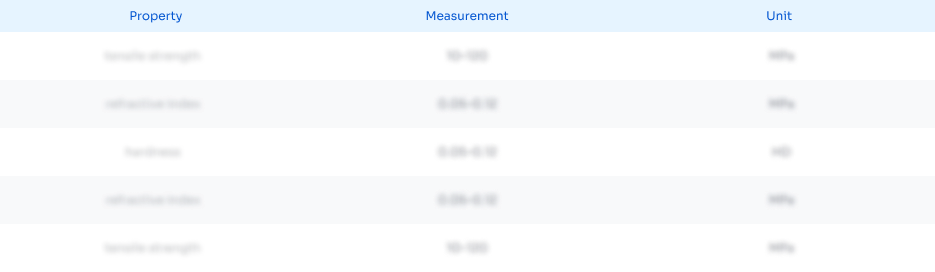
Abstract
Description
Claims
Application Information

- R&D Engineer
- R&D Manager
- IP Professional
- Industry Leading Data Capabilities
- Powerful AI technology
- Patent DNA Extraction
Browse by: Latest US Patents, China's latest patents, Technical Efficacy Thesaurus, Application Domain, Technology Topic, Popular Technical Reports.
© 2024 PatSnap. All rights reserved.Legal|Privacy policy|Modern Slavery Act Transparency Statement|Sitemap|About US| Contact US: help@patsnap.com