A stainless steel welding method
A welding method and stainless steel technology, applied in welding equipment, metal processing equipment, manufacturing tools, etc., can solve the problems of unsatisfactory, low strength, incomplete cleaning of the oxide layer on the surface of stainless steel, etc.
- Summary
- Abstract
- Description
- Claims
- Application Information
AI Technical Summary
Problems solved by technology
Method used
Image
Examples
Embodiment 1
[0027] (1) First, send the stainless steel to be welded into the laser cleaning machine for cleaning. When the laser cleaning machine cleans the stainless steel, the laser power is 300W, the laser repetition frequency is 10kHz, and the turntable speed is 30° / h during laser cleaning.
[0028] (2) Use a cutting machine to cut the welding joint of stainless steel, and then use a thousand impeller to grind the cut welding groove. The cutting machine adopts a fiber laser cutting machine, the power of the laser is 1200W, and the cutting speed of the laser is 0.8m / min, the angle of one side of the welding groove after cutting is 35-40 degrees, and the welding groove is polished 3 times with a thousand impeller after cutting.
[0029] (3), send the polished stainless steel interface to the acetone solution for soaking, and then preheat the soaked stainless steel. The acetone soaking time is 25 minutes. When soaking, use a stainless steel wire brush to clean the welding groove and weld...
Embodiment 2
[0034] (1) First, send the stainless steel to be welded into the laser cleaning machine for cleaning. When the laser cleaning machine cleans the stainless steel, the laser power is 400W, the laser repetition frequency is 10kHz, and the turntable speed is 30° / h during laser cleaning.
[0035] (2) Use a cutting machine to cut the welding joint of stainless steel, and then use a thousand impeller to grind the cut welding groove. The cutting machine adopts a fiber laser cutting machine, the power of the laser is 1200W, and the cutting speed of the laser is 0.8m / min. After cutting, the angle of the single-sided groove of the welding groove is 35-40 degrees. After cutting, the thousand impeller is used to grind the welding groove 3 times.
[0036] (3), send the polished stainless steel interface to the acetone solution for soaking, and then preheat the soaked stainless steel. The acetone soaking time is 25 minutes. When soaking, use a stainless steel wire brush to clean the welding ...
Embodiment 3
[0041] (1) First, send the stainless steel to be welded into the laser cleaning machine for cleaning. When the laser cleaning machine cleans the stainless steel, the laser power is 500W, the laser repetition frequency is 10kHz, and the turntable speed is 30° / h during laser cleaning.
[0042](2) Use a cutting machine to cut the welding joint of stainless steel, and then use a thousand impeller to grind the cut welding groove. The cutting machine adopts a fiber laser cutting machine, the power of the laser is 1200W, and the cutting speed of the laser is 0.8m / min, the angle of one side of the welding groove after cutting is 35-40 degrees, and the welding groove is polished 3 times with a thousand impeller after cutting.
[0043] (3), send the polished stainless steel interface to the acetone solution for soaking, and then preheat the soaked stainless steel. The acetone soaking time is 25 minutes. When soaking, use a stainless steel wire brush to clean the welding groove and weldi...
PUM
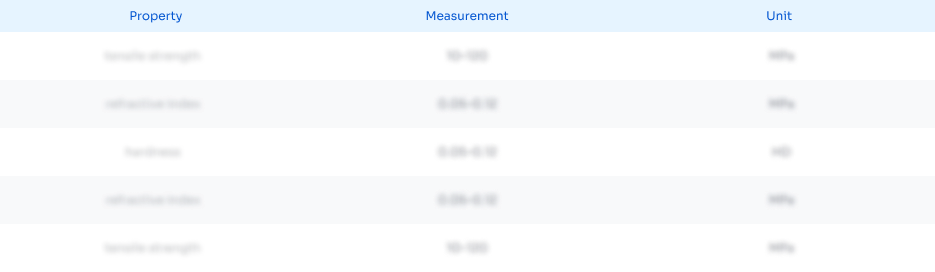
Abstract
Description
Claims
Application Information

- Generate Ideas
- Intellectual Property
- Life Sciences
- Materials
- Tech Scout
- Unparalleled Data Quality
- Higher Quality Content
- 60% Fewer Hallucinations
Browse by: Latest US Patents, China's latest patents, Technical Efficacy Thesaurus, Application Domain, Technology Topic, Popular Technical Reports.
© 2025 PatSnap. All rights reserved.Legal|Privacy policy|Modern Slavery Act Transparency Statement|Sitemap|About US| Contact US: help@patsnap.com