Woven steaple reyon fabric dyeing process
A technology of cotton cloth and technology, which is applied in the field of woven rayon dyeing technology, can solve the problems of affecting dyeing effect, fabric fluffing and pilling, affecting appearance and handle, etc., so as to improve level dyeing performance, improve whiteness, and improve fluffing The effect of pilling
- Summary
- Abstract
- Description
- Claims
- Application Information
AI Technical Summary
Problems solved by technology
Method used
Image
Examples
Embodiment 1
[0030] Embodiment 1, a kind of woven rayon dyeing process, such as figure 1 As shown, including pretreatment, dyeing and post-setting in sequence.
[0031] The pretreatment method is specifically: S1, singeing, the gray cloth is quickly passed through the combustible gas flame in the gas singeing machine to burn the fluff on the cloth; S2, oxygen bleaching, in the high temperature and high pressure overflow dyeing machine Pass through the mixture of soda ash, hydrogen peroxide and biological enzymes, and then put the cloth obtained in S1, the temperature is controlled at 90-100°C, and the time is 30-40 minutes; S3, wash the cloth obtained in S2 twice, or in a sand washing machine Put a mixture of soda ash, hydrogen peroxide, and biological enzymes into the water, and then put the fabric obtained in S1, the temperature is controlled at 95°C, and the time is 40-50 minutes; after sand washing, wash once with hot water at 80°C, and then wash once with cold water. cloth.
[0032]...
Embodiment 2-5
[0036] Embodiment 2-5: the difference of embodiment 2-5 and embodiment 1 is only, the content of sodium lauroyl taurate in the alkaline leveling agent formula in embodiment 2-5 is different, in embodiment 2-5 The parts of sodium lauroyl taurate in the basic leveling agent are respectively: 2 parts, 3 parts, 5 parts, 6 parts.
Embodiment 6-9
[0037] Embodiment 6-9: the difference of embodiment 6-9 and embodiment 1 is only, the sodium methyl cocoyl taurate content in the alkaline leveling agent formula in embodiment 6-9 is different, embodiment 6 The parts of methyl cocoyl sodium taurate in the alkaline leveling agent in -9 are respectively: 6 parts, 7 parts, 9 parts, 10 parts.
PUM
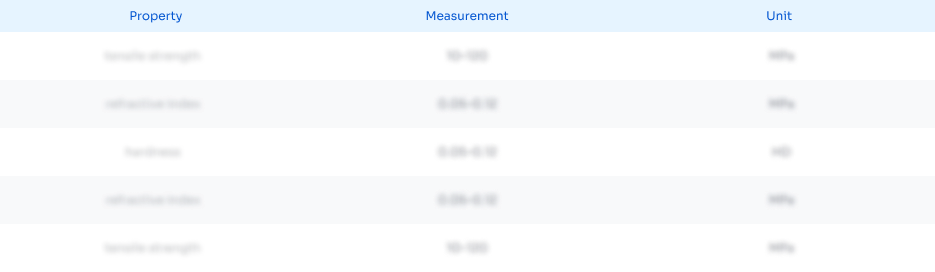
Abstract
Description
Claims
Application Information

- R&D
- Intellectual Property
- Life Sciences
- Materials
- Tech Scout
- Unparalleled Data Quality
- Higher Quality Content
- 60% Fewer Hallucinations
Browse by: Latest US Patents, China's latest patents, Technical Efficacy Thesaurus, Application Domain, Technology Topic, Popular Technical Reports.
© 2025 PatSnap. All rights reserved.Legal|Privacy policy|Modern Slavery Act Transparency Statement|Sitemap|About US| Contact US: help@patsnap.com