Ship lift intelligent control safety braking system and safety braking method thereof
A technology of safe braking and intelligent control, which is applied in the direction of vertical lifting of ship machinery, machinery of lifting ships along inclined planes, electric speed/acceleration control, etc., and can solve the impact of drive system transmission mechanical equipment, safety accidents, large braking Impact and other issues
- Summary
- Abstract
- Description
- Claims
- Application Information
AI Technical Summary
Problems solved by technology
Method used
Image
Examples
Embodiment Construction
[0070] The present invention will be further described below in conjunction with accompanying drawing:
[0071] Please refer to figure 1 , figure 2 , image 3 , an intelligent control safety braking system for a ship lift, comprising four safety braking subsystems 1, a set of transmission coordination control station 2 and a network communication module of the transmission coordination control station; wherein, the four safety braking subsystems 1 are installed On the four sets of drive mechanisms of the ship lift drive system; each safety brake system 1 includes a safety brake 1.1, a working brake 1.2, a hydraulic control pump station 1.3, a motor speed encoder 1.5 for detecting the speed of the driving motor, and a control The local electric control unit 1.9 of the hydraulic control pump station (hereinafter referred to as the local electric control unit), the motor speed encoder 1.5, the hydraulic pump station pressure detection device 1.6, and the ship lift transmissio...
PUM
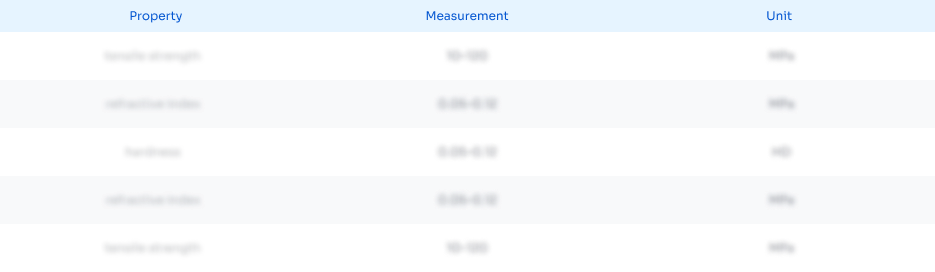
Abstract
Description
Claims
Application Information

- R&D
- Intellectual Property
- Life Sciences
- Materials
- Tech Scout
- Unparalleled Data Quality
- Higher Quality Content
- 60% Fewer Hallucinations
Browse by: Latest US Patents, China's latest patents, Technical Efficacy Thesaurus, Application Domain, Technology Topic, Popular Technical Reports.
© 2025 PatSnap. All rights reserved.Legal|Privacy policy|Modern Slavery Act Transparency Statement|Sitemap|About US| Contact US: help@patsnap.com