A kind of strip desulfurizer and preparation method thereof
A desulfurizing agent and strip-shaped technology, which is applied in the field of strip-shaped desulfurizing agent and its preparation, can solve the problems of low dispersion of binder, excessive bed pressure drop, pulverization of desulfurizing agent, etc., and reduce the resistance to crushing Effect of force difference coefficient, improvement of uniformity, and improvement of dispersion
- Summary
- Abstract
- Description
- Claims
- Application Information
AI Technical Summary
Problems solved by technology
Method used
Image
Examples
Embodiment 1
[0037] S1: Take 100 g of active zinc oxide powder and sage green powder respectively, and measure their moisture content (see Table 1 for test results). Evenly inject 2%wt steam into the active zinc oxide powder, bake the scallop powder in an oven for 1 hour, and the baking temperature is 80°C;
[0038] S2: Take a certain amount of active zinc oxide powder and scallop powder and fill them freely in a 100ml measuring cylinder respectively, and measure their bulk density (see Table 1 for test results). The active zinc oxide powder was pulverized with a ball mill for 2.5 hours, and the bulk density detection results of the active zinc oxide powder after ball milling were shown in Table 1;
[0039] S3: the activated zinc oxide powder and the safflower powder processed by S1 and S2 are added into a double-cone mixer in a weight ratio of 97:3 and mixed, and the mixing time is 1 hour;
[0040] S4: Add the active zinc oxide powder and squat powder mixed in S3 into a mixer mill for st...
Embodiment 2
[0043] S1: Take 100 g of basic zinc carbonate powder and kaolin powder respectively, and measure their moisture content (see Table 1 for test results). Evenly feed 1%wt steam into the basic zinc carbonate powder;
[0044] S2: Get a certain amount of basic zinc carbonate powder and kaolin powder and freely fill in a 100ml graduated cylinder respectively, and measure its bulk density (test results are shown in Table 1). This basic zinc carbonate powder and bulk density are that 0.40 basic zinc carbonate powder is mixed by the weight ratio of 1:2, and the bulk density detection result of the basic zinc carbonate powder after mixing is shown in Table 1;
[0045] S3: the basic zinc carbonate powder and kaolin powder processed by S1 and S2 are added into a double-cone mixer in a weight ratio of 95:5 and mixed, and the mixing time is 1.5 hours;
[0046] S4: Add the basic zinc carbonate powder and kaolin powder mixed in S3 into a mixer mill for stirring, rolling, and kneading for 30 ...
Embodiment 3
[0049] S1: Take calcium oxide powder and Portland cement powder respectively, and measure their moisture content (see Table 1 for test results). Evenly inject 1%wt steam into the Portland cement powder, bake the calcium oxide powder in an oven for 1.5 hours, and the baking temperature is 90°C;
[0050] S2: Get a certain amount of calcium oxide powder and Portland cement powder and freely fill in 100ml measuring cylinder respectively, record its bulk density (test results are shown in Table 1);
[0051] S3: the calcium oxide powder and Portland cement powder after S1, S2 treatment are added in the double-cone mixer by the weight ratio of 70:30 and mixed, and the mixing time is 2 hours;
[0052] S4: Add the calcium oxide powder and Portland cement powder mixed in S3 into a mixer mill for stirring, rolling, and kneading for 60 minutes. During the mixing process, 2% wt of the total amount of raw material powder is added to make the raw material powder Grind into a paste or mud; ...
PUM
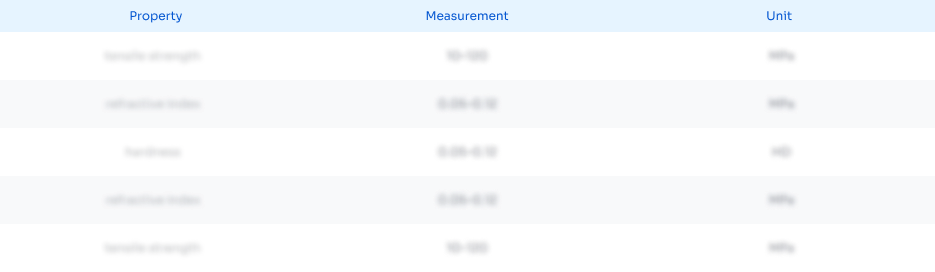
Abstract
Description
Claims
Application Information

- R&D
- Intellectual Property
- Life Sciences
- Materials
- Tech Scout
- Unparalleled Data Quality
- Higher Quality Content
- 60% Fewer Hallucinations
Browse by: Latest US Patents, China's latest patents, Technical Efficacy Thesaurus, Application Domain, Technology Topic, Popular Technical Reports.
© 2025 PatSnap. All rights reserved.Legal|Privacy policy|Modern Slavery Act Transparency Statement|Sitemap|About US| Contact US: help@patsnap.com