Method for improving visible light transmittance of vanadium dioxide film by using dilute sulfuric acid etching
A technology of vanadium dioxide and dilute sulfuric acid, applied in ion implantation plating, metal material coating process, coating and other directions, can solve the problem of visible light transmittance not meeting building requirements, etc., to improve visible light transmittance, improve Porosity, easy-to-control effects
- Summary
- Abstract
- Description
- Claims
- Application Information
AI Technical Summary
Problems solved by technology
Method used
Image
Examples
Embodiment 1
[0025] (1) Cleaning of sapphire substrate:
[0026] Put the sapphire sheet into deionized water, acetone and absolute ethanol in sequence for ultrasonic cleaning, each cleaning time is 20 minutes, to remove the inorganic and organic impurities on the surface; then wash it with deionized water, and finally clean the sapphire substrate Put into absolute ethanol for later use.
[0027] (2) Preparation of metal vanadium thin film:
[0028] The cleaned sapphire substrate is placed in the vacuum chamber of the DPS-Ⅲ ultra-high vacuum target magnetron sputtering coating machine, and the metal vanadium with a mass purity of 99.99% is used as the target material, and the argon gas with a mass purity of 99.999% is used as the target material. Working gas, background vacuum 8.0×10 -4 Pa, the argon gas flow rate is 48mL / min, the sputtering working pressure is 2Pa, the sputtering power is 120W, and the sputtering time is 8min. Repeat this step to prepare 2 samples.
[0029] (3) Preparat...
Embodiment 2
[0034] (1) Cleaning of sapphire substrate:
[0035] Put the sapphire sheet into deionized water, acetone and absolute ethanol in sequence for ultrasonic cleaning, each cleaning time is 20 minutes, to remove the inorganic and organic impurities on the surface; then wash it with deionized water, and finally clean the sapphire substrate Put into absolute ethanol for later use.
[0036] (2) Preparation of metal vanadium thin film:
[0037] The cleaned sapphire substrate is placed in the vacuum chamber of the DPS-Ⅲ ultra-high vacuum target magnetron sputtering coating machine, and the metal vanadium with a mass purity of 99.99% is used as the target material, and the argon gas with a mass purity of 99.999% is used as the target material. Working gas, background vacuum 8.0×10 -4 Pa, the argon gas flow rate is 48mL / min, the sputtering working pressure is 2Pa, the sputtering power is 120W, and the sputtering time is 8min. Repeat this step to prepare 2 samples.
[0038] (3) Preparat...
PUM
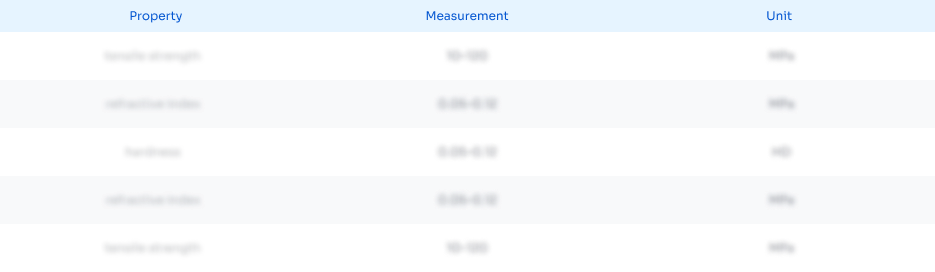
Abstract
Description
Claims
Application Information

- R&D
- Intellectual Property
- Life Sciences
- Materials
- Tech Scout
- Unparalleled Data Quality
- Higher Quality Content
- 60% Fewer Hallucinations
Browse by: Latest US Patents, China's latest patents, Technical Efficacy Thesaurus, Application Domain, Technology Topic, Popular Technical Reports.
© 2025 PatSnap. All rights reserved.Legal|Privacy policy|Modern Slavery Act Transparency Statement|Sitemap|About US| Contact US: help@patsnap.com