Production Technology of Diamond Wire Busbar Drawing Die
A wire drawing die and production process technology, applied in metal wire drawing, metal drawing forming tools, metal processing equipment, etc., can solve the problems of insufficient thermal conductivity of the sintered body 13, slow heat dissipation of the polycrystalline diamond 12, brittleness of the sintered body, etc. , to achieve the effect of improving thermal conductivity, improving filling efficiency, and reducing pressing pressure
- Summary
- Abstract
- Description
- Claims
- Application Information
AI Technical Summary
Problems solved by technology
Method used
Image
Examples
Embodiment Construction
[0025] The present invention will be described in further detail below in conjunction with the accompanying drawings.
[0026] The production process of the diamond wire bus wire drawing die includes the following steps:
[0027] Step S1 (refer to figure 1 ), forming a mold cover 11 that meets the assembly requirements through CNC lathe processing, and opening a central hole groove 14 in the center of the end face of the mold cover 11 through a laser drilling machine to obtain the mold cover 11; technical effect: manufacturing the mold cover 11 according to the actual assembly requirements , so as to improve the adaptability of the diamond wire bus wire drawing die, so that it can meet various models and different manufacturers of wire drawing machines.
[0028] S2 (reference figure 2 , image 3), mix 30% copper powder, 20% nickel powder, 10% silver powder, 3% zinc powder, 6% tungsten powder, 8% manganese powder, 21% tin powder in proportion and grind them thoroughly , t...
PUM
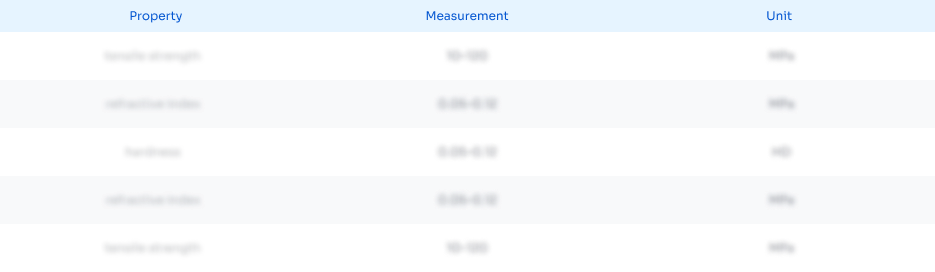
Abstract
Description
Claims
Application Information

- R&D
- Intellectual Property
- Life Sciences
- Materials
- Tech Scout
- Unparalleled Data Quality
- Higher Quality Content
- 60% Fewer Hallucinations
Browse by: Latest US Patents, China's latest patents, Technical Efficacy Thesaurus, Application Domain, Technology Topic, Popular Technical Reports.
© 2025 PatSnap. All rights reserved.Legal|Privacy policy|Modern Slavery Act Transparency Statement|Sitemap|About US| Contact US: help@patsnap.com