Ultrasonic welding device for automobile wiring harness
A technology of ultrasonic welding and wire bundles, applied in the field of machining, to achieve the effects of high fusion strength, good electrical conductivity and short welding time
- Summary
- Abstract
- Description
- Claims
- Application Information
AI Technical Summary
Problems solved by technology
Method used
Image
Examples
Embodiment 1
[0016] Embodiment one: Figure 1-Figure 3 It shows an ultrasonic welding device for automobile wire harness, which includes: a base, a push head linkage mechanism 1, a pressure head linkage mechanism 2, an ultrasonic triple device 3 and an air circuit drive device 4. The ultrasonic triple device 3 is fixed on the base, the ultrasonic triple device 3 is mainly composed of a transducer 22, a banner device 29 and a titanium alloy welding head 23 connected in sequence, and the push head linkage mechanism 1 is set On the left side of the titanium alloy welding head 23 and connected to the base, the pressure head linkage mechanism 2 is arranged on the right side of the titanium alloy welding head 23 and connected to the base, the gas circuit drives The device 4 is arranged at one end of the transducer, and is fixedly connected with the base; the ultrasonic triple device 3 is fixed on the base through a triple fixing device, and the triple fixing device includes: a triple fixing seat...
PUM
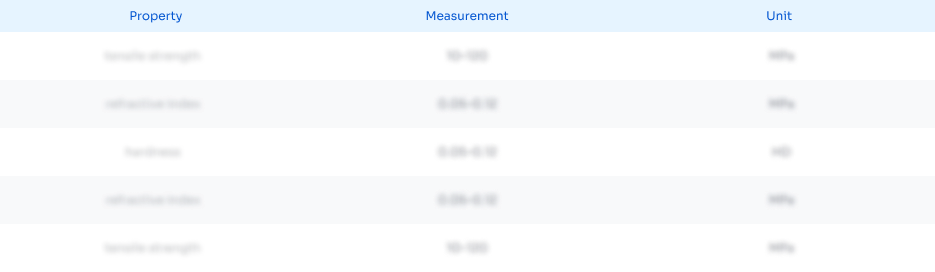
Abstract
Description
Claims
Application Information

- R&D Engineer
- R&D Manager
- IP Professional
- Industry Leading Data Capabilities
- Powerful AI technology
- Patent DNA Extraction
Browse by: Latest US Patents, China's latest patents, Technical Efficacy Thesaurus, Application Domain, Technology Topic, Popular Technical Reports.
© 2024 PatSnap. All rights reserved.Legal|Privacy policy|Modern Slavery Act Transparency Statement|Sitemap|About US| Contact US: help@patsnap.com