Flange structure transducer with vibration isolation function for ultrasonic device
A transducer and ultrasonic technology, which is applied in the field of ultrasonic tool holders and flange structure transducers, can solve the problems of ultrasonic vibration energy loss, affecting the rotation of the machine tool spindle, and low efficiency of ultrasonic processing, so as to reduce losses and avoid machine tools. Spindle damage, the effect of improving the efficiency of ultrasonic machining
- Summary
- Abstract
- Description
- Claims
- Application Information
AI Technical Summary
Problems solved by technology
Method used
Image
Examples
Embodiment 1
[0094] The present invention proposes a flange structure transducer 1 with vibration isolation function for ultrasonic devices. For the transducer in this embodiment, please refer to the appended figure 1 , 1a , 1b, and 1c, the transducer 1 includes a transducer body 10 and a flange 11 disposed on the periphery of the transducer body 10, the front end of the transducer body 10 is used to install the processing tool 5, and the flange 11 A vibration-damping structure 13 for reducing the transmission of ultrasonic vibrations from the transducer 1 to the body of the ultrasonic device is provided on the top; the vibration-damping structure 13 includes a protrusion integrally formed on the outer edge of the flange 11 and used to connect with the body of the ultrasonic device 17 , the protruding portion 17 protrudes outward along the radial direction of the flange 11 .
[0095] As shown in Table 1, based on the above-mentioned technical scheme, the connection form between the flange...
Embodiment 2
[0113] Please refer to the attached figure 2 , 2a , 2b, 2c, and 2d, this embodiment proposes a transducer 1 for an ultrasonic device, the difference from Embodiment 1 is that in this embodiment, the raised portion 17 includes several flanges 11 The protruding blocks 172 are arranged at intervals in the circumferential direction on the outer edge of the outer edge, and several protruding blocks 172 are surrounded into a ring shape surrounding the transducer body 10 . Further, an arc-shaped groove 16 is provided between two adjacent protrusions. Furthermore, the top of the bump 172 is a plane, and the top of the plane is the largest outer diameter of the flange, which is the welding position 171 for welding with the ultrasonic device body, and the welding position 171 is the position of the vibration zero point. During the transducer 1 and the ultrasonic device body, the connection position of the flange 11 and the ultrasonic device body is thus arranged at the position of th...
Embodiment 3
[0119] Please refer to the attached image 3 , 3a , 3b, 3c, and 3d, this embodiment proposes a transducer for an ultrasonic device, and its difference from Embodiment 1 is only that the raised portion 17 of this embodiment is a ring around the transducer body 10 ring shape; further, the outer diameter of the raised portion 17 gradually decreases from the middle to its two ends and forms a semicircular arc when viewed along the axial section of the transducer body 10, specifically refer to the attached Figure 3c As shown; the first damping groove structure 14 of this embodiment includes a first annular groove 141 centered on the center of the front end face of the flange 11; the second damping groove structure 15 includes the flange The center of the rear end face of 11 is the second annular groove 151 that the circle center offers; Figure 3c As shown, the first annular groove 141 and the second annular groove 151 are arranged in an offset manner, and the sum of the depths ...
PUM
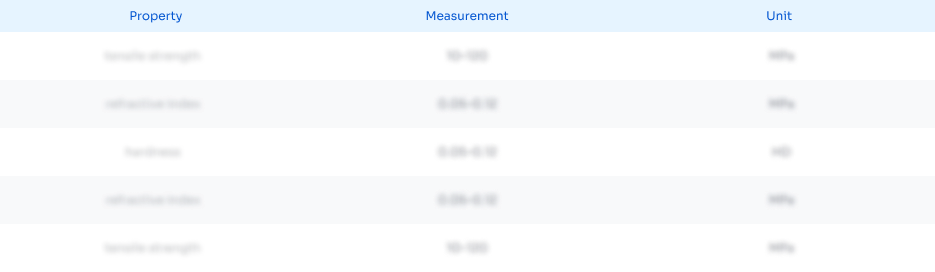
Abstract
Description
Claims
Application Information

- R&D
- Intellectual Property
- Life Sciences
- Materials
- Tech Scout
- Unparalleled Data Quality
- Higher Quality Content
- 60% Fewer Hallucinations
Browse by: Latest US Patents, China's latest patents, Technical Efficacy Thesaurus, Application Domain, Technology Topic, Popular Technical Reports.
© 2025 PatSnap. All rights reserved.Legal|Privacy policy|Modern Slavery Act Transparency Statement|Sitemap|About US| Contact US: help@patsnap.com