Hydrophilic polythiophene grafted oxidized graphene supercapacitor electrode material and preparation method thereof
A technology for supercapacitors and electrode materials, which is applied in hybrid capacitor electrodes, nanotechnology for materials and surface science, nanotechnology, etc. Effect of surface area, excellent specific capacitance
- Summary
- Abstract
- Description
- Claims
- Application Information
AI Technical Summary
Problems solved by technology
Method used
Image
Examples
Embodiment 1
[0023] (1) Add graphene oxide (25mg) into a solution of thionyl chloride (5mL), ultrasonically disperse for 40min, and then heat and reflux for 4 hours. After the reaction is completed, the excess thionyl chloride is distilled off to obtain surface acid chlorinated Graphene oxide.
[0024] (2) Hydrophilic polythiophene (n=1, 25 mg) was dissolved in anhydrous tetrahydrofuran, then acid-chlorinated graphene oxide was added, and ultrasonically dispersed for 40 min.
[0025] (3) Triethylamine (5 mL) was added into the reaction system as an acid-binding agent. The mixture was stirred and reacted at room temperature under nitrogen protection for 24 hours. After the reaction, it was centrifuged, washed with ethanol and deionized water for 3 times, and dried in vacuum for 24 hours to obtain a polythiophene (n=1) grafted graphene oxide composite material.
[0026] (4) Preparation of electrode material: Grind the composite material finely, then mix it with the mass ratio of composite m...
Embodiment 2
[0029] (1) Add graphene oxide (25 mg) into a solution of thionyl chloride (10 mL), ultrasonically disperse it for 20 minutes, and then heat and reflux for 4 hours. After the reaction is completed, the excess thionyl chloride is distilled off to obtain surface acid chlorinated Graphene oxide.
[0030] (2) Hydrophilic polythiophene (n=2, 25 mg) was dissolved in anhydrous tetrahydrofuran, followed by addition of acid-chlorinated graphene oxide, and ultrasonically dispersed for 40 min.
[0031] (3) Triethylamine (10 mL) was added into the reaction system as an acid-binding agent. The mixture was stirred and reacted at room temperature under nitrogen protection for 36 hours. After the reaction, it was centrifuged, washed with ethanol and deionized water three times, and dried in vacuum for 24 hours to obtain a graphene oxide composite material grafted with polythiophene (n=2).
[0032] (4) Preparation of electrode material: Grind the composite material finely, then mix it with the...
Embodiment 3
[0035] (1) Add graphene oxide (25 mg) into a solution of thionyl chloride (10 mL), ultrasonically disperse it for 20 minutes, and then heat and reflux for 4 hours. After the reaction is completed, the excess thionyl chloride is distilled off to obtain surface acid chlorinated Graphene oxide.
[0036] (2) Hydrophilic polythiophene (n=4, 25 mg) was dissolved in anhydrous tetrahydrofuran, followed by addition of acid-chlorinated graphene oxide, and ultrasonically dispersed for 40 min.
[0037] (3) Triethylamine (10 mL) was added into the reaction system as an acid-binding agent. The mixture was stirred and reacted at room temperature under nitrogen protection for 36 hours. After the reaction, it was centrifuged, washed with ethanol and deionized water for 3 times, and dried in vacuum for 24 hours to obtain a graphene oxide composite material grafted with polythiophene (n=4).
[0038] (4) Preparation of electrode material: Grind the composite material finely, then mix it with the...
PUM
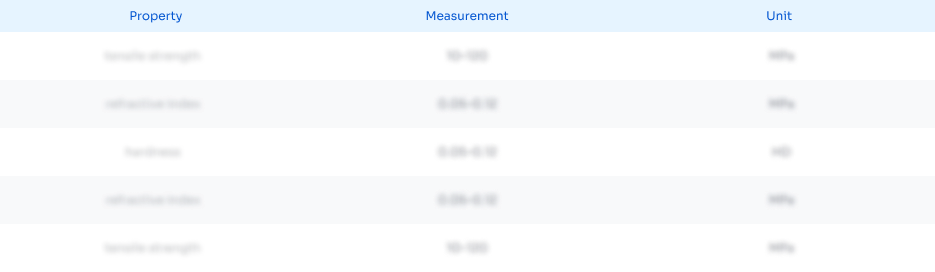
Abstract
Description
Claims
Application Information

- Generate Ideas
- Intellectual Property
- Life Sciences
- Materials
- Tech Scout
- Unparalleled Data Quality
- Higher Quality Content
- 60% Fewer Hallucinations
Browse by: Latest US Patents, China's latest patents, Technical Efficacy Thesaurus, Application Domain, Technology Topic, Popular Technical Reports.
© 2025 PatSnap. All rights reserved.Legal|Privacy policy|Modern Slavery Act Transparency Statement|Sitemap|About US| Contact US: help@patsnap.com