Straight pipe fine-drawing process
A straight tube thinning and straight tube technology, which is applied in the field of nylon straight tube thinning process, can solve the problems of high cost and development risk, and achieve the effect of reasonable design, simple principle and mass production
- Summary
- Abstract
- Description
- Claims
- Application Information
AI Technical Summary
Problems solved by technology
Method used
Image
Examples
Embodiment Construction
[0034] The present invention will be further described in detail below in conjunction with the accompanying drawings and embodiments.
[0035] This embodiment relates to the thinning process of nylon straight tube: the steps are as follows
[0036] (1) Spare parts: Prepare the straight pipe (601) and mandrel (602). The mandrel can penetrate the straight pipe. One end of the mandrel is provided with a limiting end cap to prevent the straight pipe from coming out from this end. The mandrel has a supporting thick Segment and thinning section, wherein the diameter of the thinning section is consistent with the final inner tube diameter of the straight pipe after local thinning;
[0037] (2) Preheating: Turn on the heating mechanism for heating the part of the straight pipe to be stretched, so that the heating temperature of the heating mechanism reaches 158°C±10°C;
[0038] (3) Heating: Put the mandrel through the mandrel and insert the mandrel into the nylon straight pipe, make ...
PUM
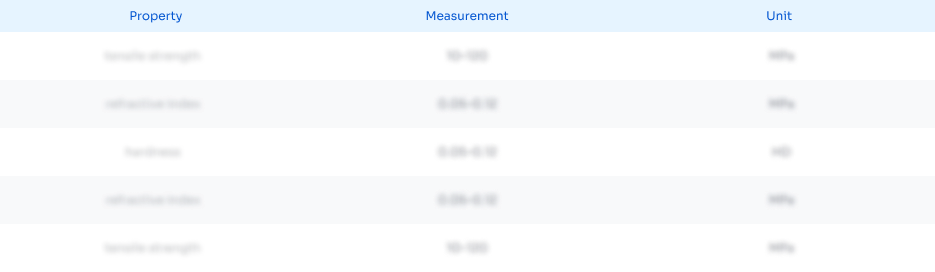
Abstract
Description
Claims
Application Information

- R&D
- Intellectual Property
- Life Sciences
- Materials
- Tech Scout
- Unparalleled Data Quality
- Higher Quality Content
- 60% Fewer Hallucinations
Browse by: Latest US Patents, China's latest patents, Technical Efficacy Thesaurus, Application Domain, Technology Topic, Popular Technical Reports.
© 2025 PatSnap. All rights reserved.Legal|Privacy policy|Modern Slavery Act Transparency Statement|Sitemap|About US| Contact US: help@patsnap.com