Lateral powder feeding head for laser cladding
A technology of laser cladding and powder feeding, which is applied in the coating process and coating of metal materials. The composition is uniform and controllable, and the effect of improving the utilization rate
- Summary
- Abstract
- Description
- Claims
- Application Information
AI Technical Summary
Problems solved by technology
Method used
Image
Examples
Embodiment 1
[0016] Cladding a layer of Al with a thickness of 0.5mm on the surface of 45 steel 2 o 3 / TiO 2 Ceramic coating, using a 3000 watt continuous fiber laser, the spot shape of the laser beam 6 is 4mm×2mm, and the inside of the independent cavity is Al 2 o 3 Powder, powder feeding speed is 2cm 3 / s, the carrier gas pressure is 0.15MPa; the second independent chamber is TiO 2 Powder, powder feeding speed is 0.8cm 3 / s, the carrier gas pressure is 0.15MPa; after laser cladding, after testing, Al with a volume ratio of 5:2 and a coefficient of variation of mixing uniformity less than 0.5% was obtained on the surface of 45 steel 2 o 3 / TiO 2 Composite ceramic coating, laser cladding quality is stable.
Embodiment 2
[0018] On the surface of 45 steel, laser 3D printing functionally graded composite parts is used. The material composition near the surface of 45 steel is WC (volume content of 5%) reinforced Mo2FeB2 composite material, which gradually transitions to the WC (volume content of 20%) on the surface. Mo2FeB2 composite material, thickness is 2mm, adopts 3000 watts continuous fiber laser, the light spot shape of laser beam 6 is 4mm×2mm, adopts the mode of layer-by-layer sintering (the first layer, the WC powder is in independent cavity 1, powder feeding speed 0.1cm 3 / min, Mo in independent chamber 2 2 FeB 2 Powder, powder feeding speed is 1.9cm 3 / min, the carrier gas pressure is 0.1MPa; the second layer, the independent chamber 1 contains WC powder, and the powder feeding speed is 0.2cm 3 / min, Mo in independent chamber 2 2 FeB 2 Powder, powder feeding speed is 1.8cm 3 / min, the carrier gas pressure is 0.1MPa; the third layer, the independent chamber 1 contains WC powder, and...
PUM
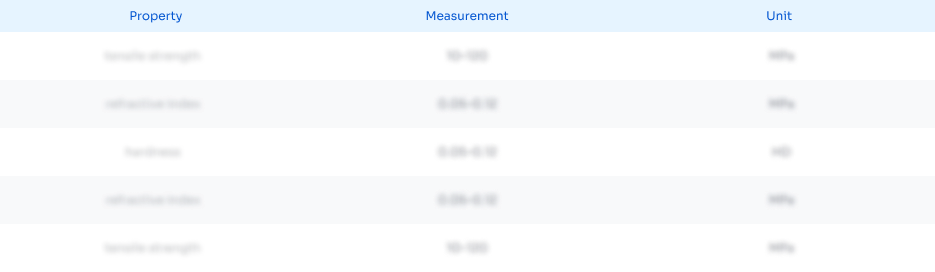
Abstract
Description
Claims
Application Information

- R&D Engineer
- R&D Manager
- IP Professional
- Industry Leading Data Capabilities
- Powerful AI technology
- Patent DNA Extraction
Browse by: Latest US Patents, China's latest patents, Technical Efficacy Thesaurus, Application Domain, Technology Topic, Popular Technical Reports.
© 2024 PatSnap. All rights reserved.Legal|Privacy policy|Modern Slavery Act Transparency Statement|Sitemap|About US| Contact US: help@patsnap.com