Embossing nano-coating preparation process and embossed panel sprayed by coating prepared by preparation process and making technology thereof
A technology of nano-coating and preparation process, which is applied in the process, coating, decorative art and other directions for producing decorative surface effects. It can solve the problems of leaving water stains, affecting the appearance, dust accumulation, etc., and achieve the effect of avoiding water stains
- Summary
- Abstract
- Description
- Claims
- Application Information
AI Technical Summary
Problems solved by technology
Method used
Examples
Embodiment 1
[0015] The technical scheme adopted in the present invention is:
[0016] A kind of embossed panel, its manufacturing process comprises the following steps:
[0017] S201 board surface cleaning;
[0018] S202 board surface etching;
[0019] S203 board surface spraying.
[0020] Among them, the S202 plate surface etching is carried out in 1mol / L hydrochloric acid solution, and the etching time is 60min.
[0021] Coating is made by following steps among the S203:
[0022] S101 with 40% (weight percent) titanium trichloride, 10% (weight percent) g-C 3 N 4 (Graphite-like carbon nitride), the balance is an ethanol mixed solution, stirred at 70°C for 70 minutes, and then dried to obtain titanium dioxide nanoparticles;
[0023] S102 Mix titanium dioxide nanoparticles and methyl acetate solution at a ratio of 1:4.2, and stir at 45° C. for 60-90 min to obtain a first mixture;
[0024] S103 the first mixture was mixed with polytetrafluoroethylene and n-butanol in a ratio of 1:1:2...
Embodiment 2
[0028] The difference between this embodiment and embodiment one is that coating is made by following steps:
[0029] S101 with 50% (weight percent) titanium trichloride, 13% (weight percent) g-C 3 N 4 (Graphite-like carbon nitride), the balance is an ethanol mixed solution, stirred at 75°C for 80min, and then dried to obtain titanium dioxide nanoparticles;
[0030] S102 Mix titanium dioxide nanoparticles and methyl acetate solution at a ratio of 1:4.2, and stir at 55° C. for 75 minutes to obtain a first mixture;
[0031] S103 the first mixture was mixed with polytetrafluoroethylene and n-butanol in a ratio of 1:1:2, and stirred at 45° C. for 100 min to obtain a second mixture;
[0032] S104 Mix the second mixture with the silicone resin at a ratio of 1:9, and stir at 110° C. for 75 minutes to obtain a third mixture;
[0033] S105 Mix the third mixture with the acrylic resin at a ratio of 2:7, and stir at room temperature to obtain a paint.
Embodiment 3
[0035] The difference between this embodiment and embodiment one is that coating is made by following steps:
[0036] S101 with 60% (weight percent) titanium trichloride, 16% (weight percent) g-C 3 N 4 (Graphite-like carbon nitride), the balance is an ethanol mixed solution, stirred at 80°C for 90min, and then dried to obtain titanium dioxide nanoparticles;
[0037] S102 Mix titanium dioxide nanoparticles and methyl acetate solution at a ratio of 1:4.2, and stir at 60° C. for 90 minutes to obtain a first mixture;
[0038] S103 the first mixture was mixed with polytetrafluoroethylene and n-butanol in a ratio of 1:1:2, and stirred at 50° C. for 120 min to obtain a second mixture;
[0039] S104 mixing the second mixture with the silicone resin at a ratio of 1:9, and stirring at 120° C. for 90 minutes to obtain a third mixture;
[0040] S105 Mix the third mixture with the acrylic resin at a ratio of 2:7, and stir at room temperature to obtain a paint.
PUM
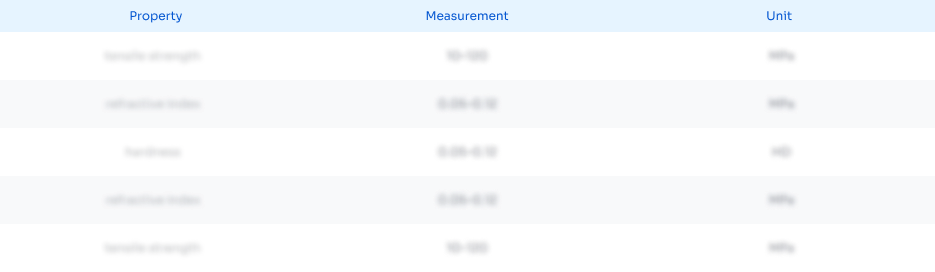
Abstract
Description
Claims
Application Information

- Generate Ideas
- Intellectual Property
- Life Sciences
- Materials
- Tech Scout
- Unparalleled Data Quality
- Higher Quality Content
- 60% Fewer Hallucinations
Browse by: Latest US Patents, China's latest patents, Technical Efficacy Thesaurus, Application Domain, Technology Topic, Popular Technical Reports.
© 2025 PatSnap. All rights reserved.Legal|Privacy policy|Modern Slavery Act Transparency Statement|Sitemap|About US| Contact US: help@patsnap.com