Method for recycling chromium in electroplating sludge through sub-molten salt method
A technology of electroplating sludge and sub-molten salt method, which is applied in the direction of improving process efficiency, can solve problems such as blanks, and achieve the effects of ensuring full contact, avoiding hardening, and being conducive to full dissolution
- Summary
- Abstract
- Description
- Claims
- Application Information
AI Technical Summary
Problems solved by technology
Method used
Examples
Embodiment 1
[0026] Get 100 kilograms of some kind of original electroplating sludge, its moisture content is about 69% according to laboratory measurement, and chromium content is 5.6% (relative to electroplating sludge dry mass). Thoroughly mix and stir 30 liters of aqueous solution containing 4.5 kg of NaOH and electroplating sludge, and dry at 60°C until the water content is lower than 20%. Put the dried material into high-temperature equipment, and bake it at 350°C for 3 hours in an air atmosphere. After the material is cooled, take it out, soak it with 150 liters of pure water for 40 minutes, filter, and rinse the filter cake with 50 liters of water to obtain a chromium solution with a concentration of about 200 liters. The chromium concentration is 7.7 grams per liter, and the recovery rate of chromium is about 89 %, to obtain about 28.1 kg of detoxified minerals, wherein the chromium content is 0.69%.
Embodiment 2
[0028] Get 20 kilograms of some kind of original electroplating sludge, its moisture content is about 33%, and chromium content is 8.9% (relative to electroplating sludge dry mass) as measured in the laboratory. Fully mix and stir 40 liters of aqueous solution containing 3.5 kilograms of KOH and the electroplating sludge to form a slurry, and then air-dry naturally until the water content is lower than 20%. Put the obtained dry material into a granulator for granulation, put the granulated pellets into a high-temperature equipment, and bake at 400° C. for 2 hours in an air atmosphere. After the material is cooled, it is taken out, leached with 85 liters of hydrochloric acid with a pH of 5 to 6 for 25 minutes, filtered, and the filter cake is rinsed with 45 liters of hydrochloric acid with a pH of 5 to 6 to obtain a chromium solution with a concentration of about 130 liters. The concentration was 8.5 g / l, the chromium recovery rate was 93%, and about 11.3 kg of detoxified miner...
Embodiment 3
[0030] Get 50 kilograms of some kind of original electroplating sludge, its water content is about 41%, chromium content is 8.2% (relative to electroplating sludge dry basis mass), calcium element mass is about 8% of dry basis sludge ( It has been proven that the use of NaOH and KOH alone or in combination will form slightly soluble calcium chromate, resulting in incomplete extraction). Will contain 4 kg NaOH and 6.5 kg Na 2 CO 3 80 liters of aqueous solution and electroplating sludge are fully mixed and stirred to form a slurry, which is dried at 50°C until the water content is lower than 20%. Put the dried material into high-temperature equipment, and bake it at 420°C for 3 hours in an air atmosphere. After the material is cooled, it is taken out, leached with 220 liters of sulfuric acid with a pH of 6 for 40 minutes, filtered, and the filter cake is rinsed with 60 liters of water to obtain a chromium solution with a concentration of about 280 liters. The chromium concentr...
PUM
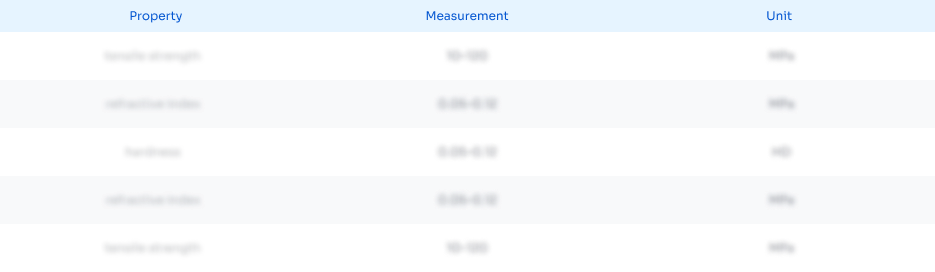
Abstract
Description
Claims
Application Information

- Generate Ideas
- Intellectual Property
- Life Sciences
- Materials
- Tech Scout
- Unparalleled Data Quality
- Higher Quality Content
- 60% Fewer Hallucinations
Browse by: Latest US Patents, China's latest patents, Technical Efficacy Thesaurus, Application Domain, Technology Topic, Popular Technical Reports.
© 2025 PatSnap. All rights reserved.Legal|Privacy policy|Modern Slavery Act Transparency Statement|Sitemap|About US| Contact US: help@patsnap.com