Preparation method for modified bentonite
A technology of bentonite and calcium-based bentonite, applied in chemical instruments and methods, inorganic chemistry, non-metallic elements, etc., can solve problems such as complicated preparation process and difficult application in industrial production
- Summary
- Abstract
- Description
- Claims
- Application Information
AI Technical Summary
Problems solved by technology
Method used
Image
Examples
preparation example 1
[0037] Preparation Example 1-Preparation of calcium-based bentonite
[0038] Mix 100g of natural calcium-based bentonite and water evenly at a mass ratio of 1:12, let it stand, and layer into supernatant, middle emulsion and lower solid sediment, and take the middle emulsion. Add water to the middle emulsion, mix evenly, let it stand, and stratify again into supernatant, middle emulsion and lower solid sedimentation. Take the middle layer emulsion obtained by layering again, and repeat washing with water to remove impurities 3 times. The middle layer emulsion obtained by the fifth water washing was centrifuged and dried to obtain 62 g of calcium-based bentonite with a montmorillonite content of 97 wt%. The composition (weight percent) of calcium-based bentonite includes Na 2 O 0.22%, K 2 O 0.066%, MgO 3.35%, CaO 1.43%, MnO 2 0.01%, SiO 2 64.6%, TiO 2 0.074%, Al 2 o 3 11.86%, FeO1.49%, Fe 2 o 3 1.44%.
Embodiment 1
[0040] (1) 5g of calcium-based bentonite (preparation example 1) is mixed with deionized water to form a calcium-based bentonite slurry with a concentration of 5wt%, and the calcium-based bentonite slurry is stirred and heated to 65 ° C, then 6g of NaCl solid is added to the In the calcium-based bentonite slurry, the first mixed solution was obtained, stirred for 5 hours, left standing, and centrifuged to obtain a crude sodium-based bentonite. The crude sodium-based bentonite was washed 4 times and dried to obtain 4.7 g of sodium-based bentonite. 3 g of sodium bentonite was mixed with deionized water to form a suspension of 2 wt % sodium bentonite, and the pH was adjusted to 4.6 with nitric acid at a concentration of 0.5 mol / L.
[0041] (2) AlCl with a concentration of 0.5mol / L 3 Aqueous solution and 0.5mol / L La(NO 3 ) 3 The aqueous solution is mixed uniformly according to the volume ratio of 5:1 to obtain the second mixed solution. The second mixed solution is heated to 40°...
Embodiment 2
[0044] (1) 5g of calcium-based bentonite (preparation example 1) is mixed with deionized water to form a calcium-based bentonite slurry with a concentration of 7wt%, and the calcium-based bentonite slurry is stirred and heated to 60°C, and then 7g of NaCl solid is added to the In the calcium-based bentonite slurry, the first mixed solution was obtained, stirred for 4 hours, allowed to stand, and centrifuged to obtain a crude sodium-based bentonite. The crude sodium-based bentonite was washed 5 times and dried to obtain 4.9 g of sodium-based bentonite. 2 g of sodium bentonite was mixed with deionized water to form a suspension of 2 wt % sodium bentonite, and the pH was adjusted to 4.3 with hydrochloric acid with a concentration of 0.3 mol / L.
[0045] (2) AlCl with a concentration of 0.4mol / L 3 Aqueous solution and CeCl with a concentration of 0.4mol / L 3 The aqueous solution is mixed uniformly according to the volume ratio of 10:1 to obtain the second mixed solution. The second...
PUM
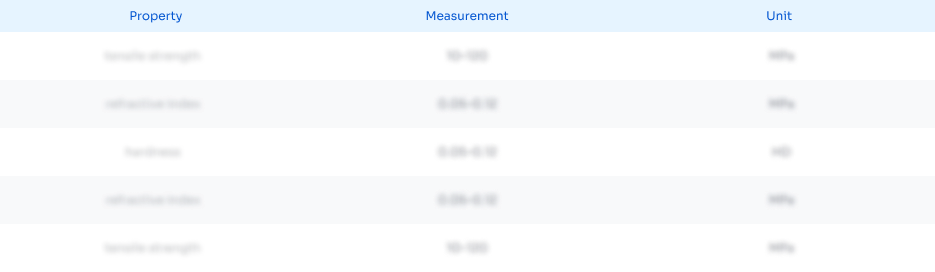
Abstract
Description
Claims
Application Information

- Generate Ideas
- Intellectual Property
- Life Sciences
- Materials
- Tech Scout
- Unparalleled Data Quality
- Higher Quality Content
- 60% Fewer Hallucinations
Browse by: Latest US Patents, China's latest patents, Technical Efficacy Thesaurus, Application Domain, Technology Topic, Popular Technical Reports.
© 2025 PatSnap. All rights reserved.Legal|Privacy policy|Modern Slavery Act Transparency Statement|Sitemap|About US| Contact US: help@patsnap.com