Method for purifying talc associated natural powder quartz and powder quartz
A purification method, quartz technology, applied in chemical instruments and methods, wet separation, solid separation, etc., can solve the problems of environmental hazards, rejection, low degree of dissociation, etc., to achieve good adaptability, short production line process, mineral processing recovery high rate effect
- Summary
- Abstract
- Description
- Claims
- Application Information
AI Technical Summary
Problems solved by technology
Method used
Image
Examples
Embodiment 1
[0096] A preparation method for talc-associated natural powder quartz, comprising the following steps:
[0097] (1) Put 800kg powdered quartz raw ore into the scrubbing machine evenly through the screw feeder to scrub and disperse. After scrubbing, the slurry enters the stirring dilution tank; the diluted slurry is screened with a rotary vibrating sieve with a sieve size of 0.125mm (120 mesh) , the under-sieve product is separated from clay minerals and iron-containing impurities through a centrifugal separator;
[0098] (2) The centrifugal underflow enters the flotation operation. First, dilute with water in the pulp preprocessor, adjust the pulp concentration to 25%, and stir for 5 minutes; feed the adjusted pulp into the flotation machine, and add 350mL collector diesel for mineralization After 3 minutes, add 35 mL of foaming agent 2-octanol, inflate and stir for 1 minute, then start to scrape the bubbles. The scraping time is 7 minutes. During the scraping process, add 2 k...
Embodiment 2
[0100] A preparation method for talc-associated natural powder quartz, comprising the following steps:
[0101](1) Put 800kg powdered quartz raw ore into the scrubbing machine evenly through the screw feeder to scrub and disperse. After scrubbing, the slurry enters the stirring dilution tank; the diluted slurry is screened with a rotary vibrating sieve with a sieve size of 0.125mm (120 mesh) , the under-sieve product is separated from clay minerals and iron-containing impurities through a centrifugal separator;
[0102] (2) The centrifugal underflow enters the flotation operation. First, dilute with water in the pulp preprocessor, adjust the pulp concentration to 23%, and stir for 5 minutes; feed the adjusted pulp into the flotation machine, and add 400mL of collector diesel for mineralization After 3 minutes, add 40 mL of foaming agent 2-octanol, inflate and stir for 1 minute, then start to scrape the bubbles. The scraping time is 7 minutes. During the scraping process, add 2...
Embodiment 3
[0104] A preparation method for talc-associated natural powder quartz, comprising the following steps:
[0105] (1) Put 800kg powdered quartz raw ore into the scrubbing machine evenly through the screw feeder to scrub and disperse. After scrubbing, the slurry enters the stirring dilution tank; the diluted slurry is screened with a rotary vibrating sieve with a sieve size of 0.125mm (120 mesh) , the under-sieve product is separated from clay minerals and iron-containing impurities through a centrifugal separator;
[0106] (2) The centrifugal underflow enters the flotation operation. First, dilute with water in the pulp preprocessor, adjust the pulp concentration to 20%, and stir for 10 minutes; feed the adjusted pulp into the flotation machine, and add 900mL of collector diesel for mineralization After 3 minutes, add 90mL of foaming agent 2-octanol, inflate and stir for 1 minute and start scraping for 7 minutes. During the scraping process, add 2kg of cleaning water. Separatio...
PUM
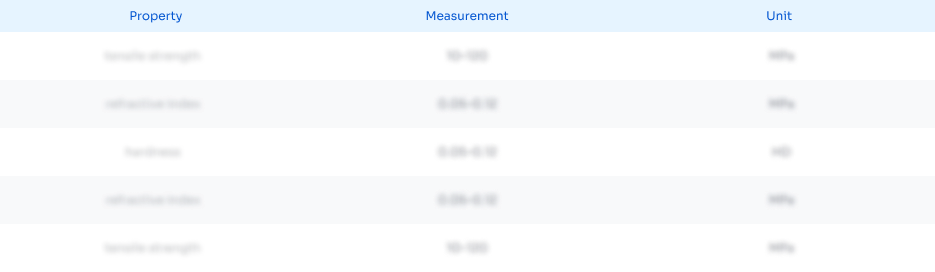
Abstract
Description
Claims
Application Information

- R&D
- Intellectual Property
- Life Sciences
- Materials
- Tech Scout
- Unparalleled Data Quality
- Higher Quality Content
- 60% Fewer Hallucinations
Browse by: Latest US Patents, China's latest patents, Technical Efficacy Thesaurus, Application Domain, Technology Topic, Popular Technical Reports.
© 2025 PatSnap. All rights reserved.Legal|Privacy policy|Modern Slavery Act Transparency Statement|Sitemap|About US| Contact US: help@patsnap.com