Digital printing method for increasing color depth of cotton fabric printing pattern
A digital printing and cotton fabric technology, applied in dyeing, textiles and papermaking, etc., can solve the problems of edge bleeding of patterns and insufficient color depth of patterns printed with paste, and achieve low water holding capacity and strong wet friction The effect of good degree and high viscosity
- Summary
- Abstract
- Description
- Claims
- Application Information
AI Technical Summary
Problems solved by technology
Method used
Image
Examples
preparation example Construction
[0031] The preparation process of digital printing pretreatment sizing agent is as follows: first, add the digital printing paste into distilled water to fully soak, stir at high speed to form a paste, and the stirring speed is 1200-1500r / min, then add alkali agent and oxidant, stir evenly, measure the viscosity, Keep the viscosity not lower than 10,000mPa, and you can get an environmentally friendly and degradable digital printing pretreatment sizing agent.
[0032] Step 2, inkjet printing:
[0033] 2.1 Ink-jet printing the cotton fabric after the pretreatment in step 1, and drying at a temperature of 90-100°C;
[0034] 2.2 Steam the dried printed fabric under saturated steam for 5-10 minutes, then wash in cold water, soap, hot water, and dry in sequence to complete the printing of cotton fabric.
[0035] Among them, cold water washing refers to cleaning with normal temperature water; soap washing liquid is soap powder aqueous solution, soap powder is soap powder for industr...
Embodiment 1
[0042] Step 1, weigh according to mass percentage: carboxypolyvinyl alcohol 4%, anti-staining salt S 1%, distilled water 95%, add polyvinyl alcohol to distilled water and fully soak, stir at a high speed to form a paste, the stirring speed is 1200r / min, and then Add anti-dyeing salt S, stir evenly, measure the viscosity, keep the viscosity not lower than 10000mPa, and then get an environmentally friendly and degradable digital printing pretreatment sizing agent.
[0043] Step 2, pre-printing treatment of cotton fabric:
[0044] The digital printing pretreatment sizing agent is scraped on one side of the cotton fabric, and the amount of the digital printing pretreatment sizing agent is 1% of the mass of the cotton fabric; then the cotton fabric after the sizing agent is scraped and dried at a temperature of 90 ° C.
[0045] Step 3, inkjet printing:
[0046] 3.1 Inkjet printing the cotton fabric after the pretreatment in step 1, and drying at a temperature of 90°C;
[0047] 3....
Embodiment 2
[0049] Step 1, weigh according to mass percentage: carboxymethyl polysaccharide polymer 5%, anti-staining salt S 0.2%, sodium hydroxide 2%, distilled water 92.8%, add carboxymethyl polysaccharide polymer to distilled water to fully soak and stir at high speed To form a paste, the stirring speed is 1250r / min, then add sodium hydroxide and anti-staining salt S, stir evenly, measure the viscosity, keep the viscosity not lower than 10000mPa, and obtain an environmentally friendly and degradable digital printing pretreatment sizing agent.
[0050] Step 2, pre-printing treatment of cotton fabric:
[0051] The digital printing pretreatment sizing agent is scraped on one side of the cotton fabric, and the amount of the digital printing pretreatment sizing agent is 2% of the quality of the cotton fabric; then the cotton fabric after the scraping sizing agent is dried at a temperature of 92 ° C.
[0052] Step 3, inkjet printing:
[0053] 3.1 Inkjet printing the cotton fabric after the ...
PUM
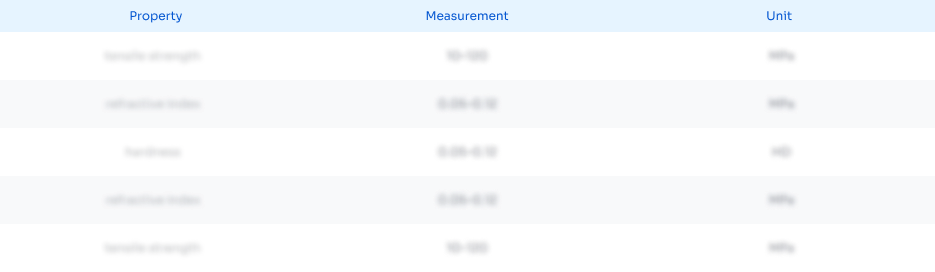
Abstract
Description
Claims
Application Information

- R&D Engineer
- R&D Manager
- IP Professional
- Industry Leading Data Capabilities
- Powerful AI technology
- Patent DNA Extraction
Browse by: Latest US Patents, China's latest patents, Technical Efficacy Thesaurus, Application Domain, Technology Topic, Popular Technical Reports.
© 2024 PatSnap. All rights reserved.Legal|Privacy policy|Modern Slavery Act Transparency Statement|Sitemap|About US| Contact US: help@patsnap.com