Flame-retardant polyurethane foam plastic and preparation method thereof
A technology of foam plastics and polyurethane, applied in the field of flame-retardant polyurethane foam plastics, can solve the problems of polyurethane foam materials such as decreased compressive strength, poor compatibility, and unsustainable flame-retardant performance, and achieve low cost, good controllability, The effect of simple process operation
- Summary
- Abstract
- Description
- Claims
- Application Information
AI Technical Summary
Problems solved by technology
Method used
Image
Examples
Embodiment 1
[0020] 48 parts of diphenylmethane diisocyanate, 52 parts of polyether polyol, 2 parts of water, 0.24 parts of triethylenediamine, 0.4 parts of dibutyltin dilaurate, 0.5 parts of methyl silicone oil 201, lignin-diisocyanate-polyphosphoric acid Add 20 parts of ammonium (the mass ratio of lignin / diisocyanate / ammonium polyphosphate is 1:0.2:1) to the reactor at one time, mix and foam under high-speed stirring conditions to obtain flame-retardant polyurethane foam.
Embodiment 2
[0022] 35 parts of toluene diisocyanate, 65 parts of polyether polyol, 1.5 parts of water, 0.4 parts of triethanolamine, 0.45 parts of dibutyltin dilaurate, 0.45 parts of methyl silicone oil 201, lignin-diisocyanate-ammonium polyphosphate (lignin / The mass ratio of diisocyanate / ammonium polyphosphate is 1:0.25:1.1) Add 30 parts into the reactor at one time, mix and foam under high-speed stirring conditions to obtain flame-retardant polyurethane foam.
Embodiment 3
[0024] 40 parts of hexamethylene diisocyanate, 60 parts of polyether polyol, 2.5 parts of water, 0.35 parts of triethanolamine, 0.42 parts of dibutyltin dilaurate, 0.45 parts of methyl silicone oil 201, lignin-diisocyanate-ammonium polyphosphate ( The mass ratio of lignin / diisocyanate / ammonium polyphosphate is 1:0.2:1.2) 35 parts are added into the reactor at one time, mixed and foamed under high-speed stirring conditions to obtain flame-retardant polyurethane foam.
PUM
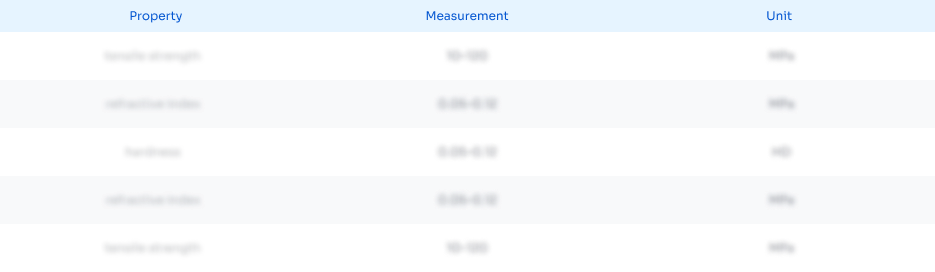
Abstract
Description
Claims
Application Information

- R&D Engineer
- R&D Manager
- IP Professional
- Industry Leading Data Capabilities
- Powerful AI technology
- Patent DNA Extraction
Browse by: Latest US Patents, China's latest patents, Technical Efficacy Thesaurus, Application Domain, Technology Topic, Popular Technical Reports.
© 2024 PatSnap. All rights reserved.Legal|Privacy policy|Modern Slavery Act Transparency Statement|Sitemap|About US| Contact US: help@patsnap.com