Annular shear type deflection electric acceleration sensor and laminated structure acceleration sensor
An acceleration sensor and circular shearing technology, applied in the field of sensors, can solve the problems of inconvenient acceleration sensors, poor stability of pressure sensors, and affecting test accuracy, etc., and achieve the effects of improving sensitivity, increasing signal amplitude, and convenient design
- Summary
- Abstract
- Description
- Claims
- Application Information
AI Technical Summary
Problems solved by technology
Method used
Image
Examples
Embodiment Construction
[0026] The present invention will be described in further detail below in conjunction with the accompanying drawings and specific embodiments.
[0027] as attached Figure 1-2 As shown, the present invention discloses an annular shear type flexoelectric acceleration sensor, comprising a support rod 5, an output terminal 7, an annular mass block 2 and an annular sensitive block 3, and the annular sensitive block 3 is made of a flexoelectric dielectric material It is preferably a non-polarized strontium barium titanate ring with a thickness of 5 mm and a height of 1 mm. The inner and outer rings of the ring are coated with a metal film layer 1. The metal film layer 1 is deposited by evaporation. Usually A gold film with a thickness of 10nm is used as the output electrode of the flexoelectric dielectric material.
[0028] Annular mass 2 is preferably 8mm thick, 1mm high tungsten ring, the inner ring of annular sensitive block 3 is fixed on the upper end of support rod 5, the inn...
PUM
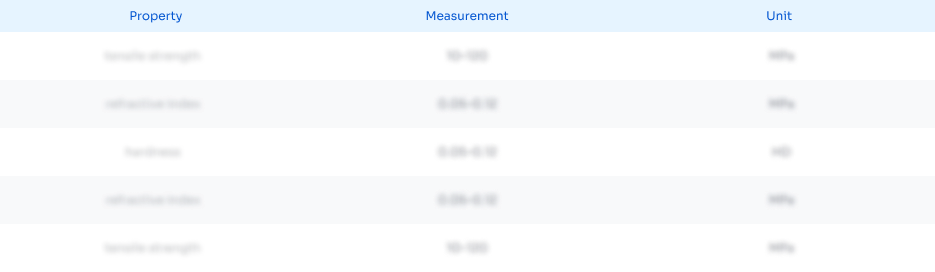
Abstract
Description
Claims
Application Information

- R&D
- Intellectual Property
- Life Sciences
- Materials
- Tech Scout
- Unparalleled Data Quality
- Higher Quality Content
- 60% Fewer Hallucinations
Browse by: Latest US Patents, China's latest patents, Technical Efficacy Thesaurus, Application Domain, Technology Topic, Popular Technical Reports.
© 2025 PatSnap. All rights reserved.Legal|Privacy policy|Modern Slavery Act Transparency Statement|Sitemap|About US| Contact US: help@patsnap.com