Surface treatment method of dry-jet wet-spun carbon fibers
A technology of dry jet wet spinning and surface treatment, which is applied in fiber treatment, carbon fiber, textiles and paper making, etc. It can solve the problems of reduced surface activity, difficulty in compounding, and low bonding performance, and achieves the effect of easy operation
- Summary
- Abstract
- Description
- Claims
- Application Information
AI Technical Summary
Problems solved by technology
Method used
Image
Examples
Embodiment 1
[0025] The carbon fiber was passed through an electrolytic cell filled with 30 ℃, 1mol / L ammonium bicarbonate aqueous solution, the passing time was 70s, and the current density was adjusted to 2.46A m -2 , the electrode spacing is 250mm, cleaned at room temperature and dried at 100℃, and then doped with 3% mass fraction of monodisperse nano-TiO 2 The water-based epoxy sizing agent is used for sizing and then winding.
Embodiment 2
[0027] The carbon fiber was passed through an electrolytic cell filled with 30 ℃, 1mol / L ammonium bicarbonate aqueous solution, the passing time was 70s, and the current density was adjusted to 7.38A m -2 , the electrode spacing was 250 mm, cleaned at room temperature, dried at 100 °C, and then doped with 5% mass fraction of monodisperse nano-TiO 2 The water-based epoxy sizing agent is used for sizing and then winding.
Embodiment 3
[0029] The carbon fiber was passed through an electrolytic cell filled with 28 ℃, 1mol / L ammonium bicarbonate aqueous solution, the passing time was 70s, and the current density was adjusted to 2.11A m -2 , the electrode spacing is 270mm, cleaned at room temperature, dried at 100°C, and then sized and rolled.
PUM
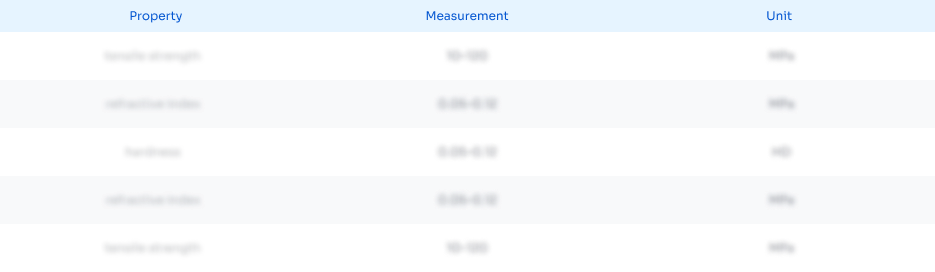
Abstract
Description
Claims
Application Information

- R&D
- Intellectual Property
- Life Sciences
- Materials
- Tech Scout
- Unparalleled Data Quality
- Higher Quality Content
- 60% Fewer Hallucinations
Browse by: Latest US Patents, China's latest patents, Technical Efficacy Thesaurus, Application Domain, Technology Topic, Popular Technical Reports.
© 2025 PatSnap. All rights reserved.Legal|Privacy policy|Modern Slavery Act Transparency Statement|Sitemap|About US| Contact US: help@patsnap.com