Use method of die cutting welding fusion equipment
A combination of equipment and die-cutting technology, applied in metal processing, etc., can solve problems such as high scrap rate and uneven folding force, and achieve the effect of improving folding quality, folding efficiency and quality, and ingenious design concept
- Summary
- Abstract
- Description
- Claims
- Application Information
AI Technical Summary
Problems solved by technology
Method used
Image
Examples
Embodiment 1
[0021] This embodiment involves a method of using die-cutting welding fusion equipment, which is realized through the following technical solutions:
[0022] The method of using the die-cutting welding fusion equipment is divided into two parts. First, the PET film is stamped and cut by the flat punching forming equipment, and then the cut PET film is folded and thermally bonded by the high-frequency welding equipment; this embodiment When the high-frequency welding equipment involved is in use, the specific operation steps are as follows:
[0023] S1. Turn on the main power supply 1 of the machine, the display screen lights up, adjust the appropriate height of the upper mold 5 by setting the button 4, and install the lower mold 7;
[0024] S2. Connect the suction to the mold suction outlet 9, set the suction parameters in the setting button 4, that is, adjust the wind speed according to the material of the heat connection;
[0025] S3. Operate the rocker arm 20 to snap the s...
PUM
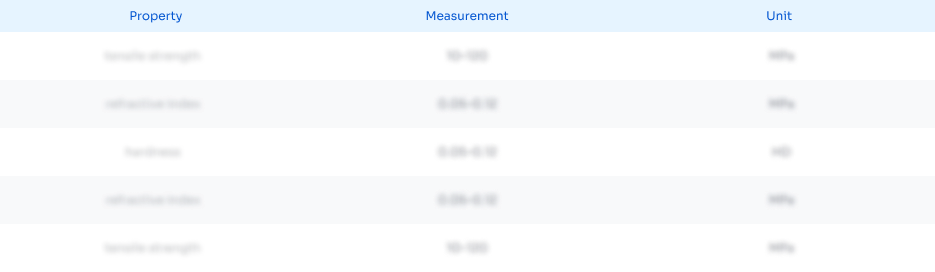
Abstract
Description
Claims
Application Information

- R&D
- Intellectual Property
- Life Sciences
- Materials
- Tech Scout
- Unparalleled Data Quality
- Higher Quality Content
- 60% Fewer Hallucinations
Browse by: Latest US Patents, China's latest patents, Technical Efficacy Thesaurus, Application Domain, Technology Topic, Popular Technical Reports.
© 2025 PatSnap. All rights reserved.Legal|Privacy policy|Modern Slavery Act Transparency Statement|Sitemap|About US| Contact US: help@patsnap.com