Method for treating mercury tailings adopting oxidation leaching
A technology for leaching and tailings, applied in the fields of metallurgy and environmental protection, can solve the problems of difficulty in large-scale application, high cost, and high processing cost, and achieve the effects of reducing disposal costs, fast leaching, and low operating costs.
- Summary
- Abstract
- Description
- Claims
- Application Information
AI Technical Summary
Problems solved by technology
Method used
Examples
Embodiment 1
[0025] Oxidant TCCA and pH adjuster hydrochloric acid are dissolved in water, make leaching solution, the concentration of TCCA in the leaching solution is 0.5g / L, and the concentration of HCl is 3g / L;
[0026] The mercury tailings used are the flotation tailings obtained by the flotation process of mercury mines. The mercury content is 118g / t, and 87.4% of the particles are smaller than 150μm. The main gangue components are quartz and dolomite. Mercury exists in the form of cinnabar. Grinding treatment is required;
[0027] Put the mercury tailings in the leaching solution, leaching under stirring conditions, the leaching time is 10min, and the leaching material is obtained after the leaching is completed; the amount of mercury tailings added in each liter of leaching solution is 0.4kg, that is, 1kg of mercury tailings is placed in In 2.5L leaching solution;
[0028] Filter the leached material to separate the leached residue and the leached liquid; the leached residue is a ...
Embodiment 2
[0032] Method is with embodiment 1, and difference is:
[0033] (1) The concentration of TCCA in the leaching solution is 1g / L, and the concentration of HCl is 3.5g / L; the mercury tailings used are the flotation tailings obtained by the mercury mine flotation process, and the mercury content is 187g / t, 83.5 % of the particles are less than 150μm, the main gangue components are quartz and dolomite, mercury exists in the form of cinnabar, and does not need to be ground;
[0034] (2) The leaching time is 15 minutes; the leaching residue contains 0.03mg / L of mercury, and the leaching solution contains 71.6mg / L of mercury as measured by the toxicity leaching test, and the leaching rate of mercury reaches 95.7%;
[0035] (3) Ferrous sulfide is 40% of the total mass of TCCA, and the precipitation reaction time is 35 minutes; the solid content in the precipitation contains 18.7% mercury by mass percentage, and the precipitation rate of mercury is greater than 99%.
Embodiment 3
[0037] Method is with embodiment 1, and difference is:
[0038] (1) The concentration of TCCA in the leaching solution is 1.5g / L, and the concentration of HCl is 4.5g / L; the mercury tailings used are the flotation tailings obtained by the mercury mine flotation process, and the mercury content is 306g / t. 71.0% of the particles are smaller than 150μm, the main gangue components are quartz and dolomite, mercury exists in the form of cinnabar, and does not need to be ground;
[0039] (2) The leaching time is 15 minutes; the addition amount of mercury tailings in each liter of leaching solution is 0.2kg, that is, 1kg of mercury tailings is placed in 5L of leaching solution; Mercury content is 57.2mg / L, and the mercury leaching rate reaches 93.4%;
[0040] (3) Ferrous sulfide is 25% of the total mass of TCCA, and the precipitation reaction time is 40 minutes; the solid content in the precipitation contains 17.1% mercury by mass percentage, and the precipitation rate of mercury is ...
PUM
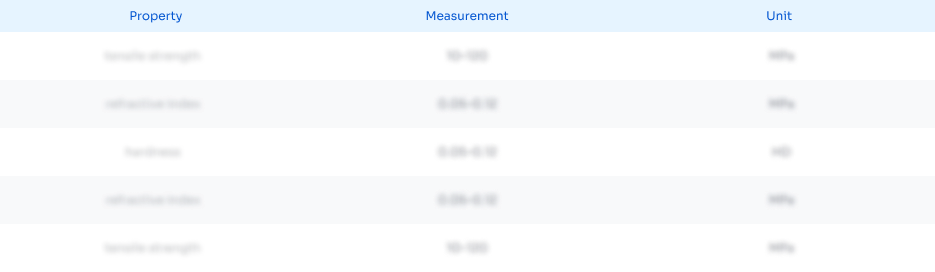
Abstract
Description
Claims
Application Information

- R&D Engineer
- R&D Manager
- IP Professional
- Industry Leading Data Capabilities
- Powerful AI technology
- Patent DNA Extraction
Browse by: Latest US Patents, China's latest patents, Technical Efficacy Thesaurus, Application Domain, Technology Topic, Popular Technical Reports.
© 2024 PatSnap. All rights reserved.Legal|Privacy policy|Modern Slavery Act Transparency Statement|Sitemap|About US| Contact US: help@patsnap.com