A kind of solar battery backboard waste film and its leftover material reutilization method
A technology of solar cells and leftover materials, which is applied in the field of plastic resource recycling, can solve the problems of being unable to be incinerated and landfilled, having no commercial application value, and low mechanical properties of materials, so as to save non-renewable resources and solve compatibility problems. Good, cost-effective effect
- Summary
- Abstract
- Description
- Claims
- Application Information
AI Technical Summary
Problems solved by technology
Method used
Image
Examples
Embodiment 1
[0035]Get 87.5g of crushed and dried solar cell backplane waste film fragments, 10g of ethylene-vinyl acetate copolymer (EVA), 1g of MMA-GMA-St, 0.5g of antioxidant 1010 and 1g of calcium stearate into a mixer and mix Uniform, then added to the twin-screw extruder for blending, the temperature of each zone of the screw from the feed port to the head is 200°C, 230°C, 240°C, 250°C, 240°C, 245°C, 250°C, 245°C , 245°C, 250°C, screw speed 300rpm, react the recycled solar cell backsheet waste film fragments with ethylene-vinyl acetate and high-efficiency compatibilizer, then extrude and cool, and pelletize to prepare alloy materials.
Embodiment 2
[0037] Get 85.5g pulverized and dried solar battery backplane waste film fragments, 8g ethylene-vinyl acetate copolymer (EVA), 5gMMA-GMA-St, 0.5g antioxidant 1010 and 1g calcium stearate drop into mixer Mix evenly, then add to the twin-screw extruder for blending, the temperature of each zone of the screw from the feeding port to the machine head is 200°C, 230°C, 240°C, 250°C, 240°C, 245°C, 250°C, 245°C ℃, 245℃, 250℃, screw speed 300rpm, make the recycled solar battery back sheet waste film fragments react with ethylene-vinyl acetate and high-efficiency compatibilizer, then extrude and cool, and pelletize to prepare the alloy material .
Embodiment 3
[0039] Get 82.5g pulverized and dried solar cell backplane waste film fragments, 8g ethylene-vinyl acetate copolymer (EVA), 8gMMA-GMA-St, 0.5g antioxidant 1010 and 1g calcium stearate drop into mixer Mix evenly, then add to the twin-screw extruder for blending, the temperature of each zone of the screw from the feeding port to the machine head is 200°C, 230°C, 240°C, 250°C, 240°C, 245°C, 250°C, 245°C ℃, 245℃, 250℃, screw speed 300rpm, make the recycled solar battery back sheet waste film fragments react with ethylene-vinyl acetate and high-efficiency compatibilizer, then extrude and cool, and pelletize to prepare the alloy material .
PUM
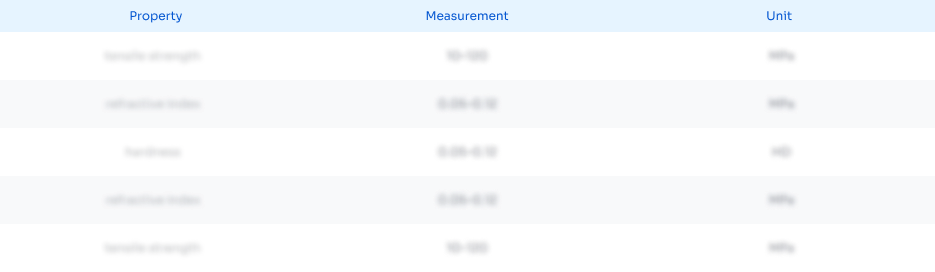
Abstract
Description
Claims
Application Information

- R&D
- Intellectual Property
- Life Sciences
- Materials
- Tech Scout
- Unparalleled Data Quality
- Higher Quality Content
- 60% Fewer Hallucinations
Browse by: Latest US Patents, China's latest patents, Technical Efficacy Thesaurus, Application Domain, Technology Topic, Popular Technical Reports.
© 2025 PatSnap. All rights reserved.Legal|Privacy policy|Modern Slavery Act Transparency Statement|Sitemap|About US| Contact US: help@patsnap.com