Electronic cigarette atomizer porous ceramic, preparation method thereof, and electronic cigarettes provided with electronic cigarette atomizer porous ceramic
An electronic cigarette vaporizer and porous ceramic technology, applied in the field of electronic cigarettes, can solve the problems of affecting the experience, prone to oil leakage, and easy to drop fine particles, so as to enhance the performance of oil absorption and oil locking, and ensure the quality of finished products.
- Summary
- Abstract
- Description
- Claims
- Application Information
AI Technical Summary
Problems solved by technology
Method used
Image
Examples
Embodiment 1
[0043] A method for preparing porous ceramics for an electronic atomizer, comprising the following steps:
[0044] Step 1, select diatomite 80Kg of natural porous material for use, the average pore diameter of diatomite is 5um, add it to the mixer, then add particle size and be 20Kg of pore-forming agent graphite powder of 300 objects, then mix diatomite and graphite Stir and mix the powder pore-forming agent evenly to obtain a powder;
[0045] Step 2. Put the uniformly mixed powder in step 1 into a rubber sleeve, seal it well, put it into a cold isostatic press, control the pressure at 100MPa, keep the pressure for 10 minutes, and then take out the pressed compact.
[0046] Step 3: Put the block into a heating furnace, heat it to 1200°C at a heating rate of 1°C / min, keep it warm for 5 hours, and completely burn off the pore-forming agent in the block, so as to obtain a porous ceramic skeleton prefabricated body.
[0047] Step 4: Use a roller ball mill to crush the obtained p...
Embodiment 2
[0055] A method for preparing porous ceramics for an electronic atomizer, comprising the following steps:
[0056] Step 1, select 50Kg of diatomite of natural porous material, the average pore size of diatomite is 200um, add it to the mixer, and then add 50Kg of pore-forming agent charcoal with a particle size of 100, and then diatomite and graphite powder The pore-forming agent is stirred and mixed evenly to obtain a powder;
[0057] Step 2. Put the uniformly mixed powder in step 1 into a rubber sleeve, seal it well, put it into a cold isostatic press, control the pressure at 50MPa, keep the pressure for 2 minutes, and then take out the pressed compact.
[0058] Step 3: Put the block into a heating furnace, heat it to 700°C at a heating rate of 5°C / min, keep it warm for 1 hour, and completely burn off the pore-forming agent in the block to obtain a porous ceramic skeleton prefabricated body.
[0059] Step 4: Use a roller ball mill to crush the obtained porous ceramic skeleto...
Embodiment 3
[0067] A method for preparing porous ceramics for an electronic atomizer, comprising the following steps:
[0068] Step 1. Select 60Kg of diatomite which is a natural porous material. The average pore size of diatomite is 100um. Add it to the mixer, then add 40Kg of pore-forming agent cellulose with a particle size of 200 meshes, and then mix diatomite and graphite Stir and mix the powder pore-forming agent evenly to obtain a powder;
[0069] Step 2. Put the uniformly mixed powder in step 1 into a rubber sleeve, seal it well, put it into a cold isostatic press, control the pressure at 80MPa, keep the pressure for 8 minutes, and then take out the pressed compact.
[0070] Step 3: Put the block into a heating furnace, heat it to 950°C at a heating rate of 3°C / min, keep it warm for 3 hours, and completely burn off the pore-forming agent in the block, so as to obtain a porous ceramic skeleton prefabricated body.
[0071] Step 4: Use a roller ball mill to crush the obtained porous...
PUM
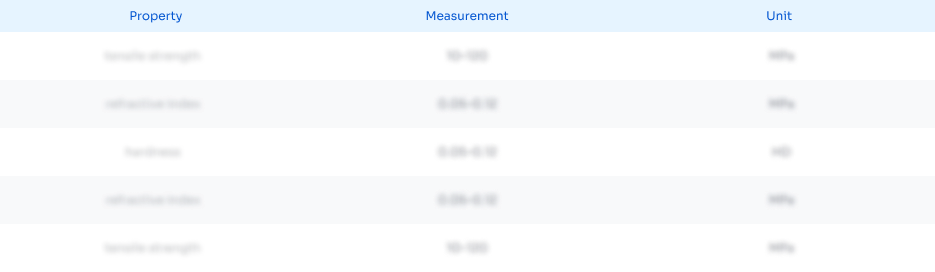
Abstract
Description
Claims
Application Information

- Generate Ideas
- Intellectual Property
- Life Sciences
- Materials
- Tech Scout
- Unparalleled Data Quality
- Higher Quality Content
- 60% Fewer Hallucinations
Browse by: Latest US Patents, China's latest patents, Technical Efficacy Thesaurus, Application Domain, Technology Topic, Popular Technical Reports.
© 2025 PatSnap. All rights reserved.Legal|Privacy policy|Modern Slavery Act Transparency Statement|Sitemap|About US| Contact US: help@patsnap.com