Method for preparing anti-oxidative polyamide reverse osmosis membrane
A technology of oxidizing polyamide and reverse osmosis membrane, which is applied in chemical instruments and methods, reverse osmosis, semi-permeable membrane separation, etc., can solve the problem that it is difficult to achieve large-scale production, affects the membrane flux and sodium chloride removal rate, and the material ADMH is difficult to achieve. Obtaining and other issues to achieve the effect of improving antioxidant performance, cost saving, and ensuring removal rate
- Summary
- Abstract
- Description
- Claims
- Application Information
AI Technical Summary
Problems solved by technology
Method used
Image
Examples
Embodiment 1
[0028] The production method of anti-oxidation polyamide reverse osmosis membrane is as follows:
[0029] 1. Preparation of aqueous phase liquid: same as comparative example.
[0030] 2. The preparation of the oil phase solution: the same as the comparative example.
[0031] 3. Preparation of post-grafting treatment solution: Weigh 6 g of glutaraldehyde and add it to 1992 g of deionized water. After stirring for 5 minutes, add 2 g of tannic acid and continue stirring for 10 minutes to obtain a post-grafting treatment solution.
[0032] 4. Prepare the nascent reverse osmosis membrane with the same method as the comparative example, then immerse the nascent reverse osmosis membrane in the post-grafting treatment solution for 2 minutes, and finally dry the membrane in a 60°C oven for 3 minutes to obtain the antioxidant aromatic polymer Amide reverse osmosis membrane.
[0033] The membrane detection method is the same as that of the comparative example, and the results are shown...
Embodiment 2
[0035] The production method of anti-oxidation polyamide reverse osmosis membrane is as follows:
[0036] 1. Preparation of aqueous phase liquid: same as comparative example.
[0037] 2. The preparation of the oil phase solution: the same as the comparative example.
[0038] 3. Preparation of post-grafting treatment solution: Weigh 4 g of glyoxal and add it to 1992 g of deionized water, stir for 5 minutes, add 4 g of nitric acid, and continue stirring for 10 minutes to obtain a post-grafting treatment solution.
[0039] 4, film making method is the same as embodiment 1
[0040] The membrane detection method is the same as that of the comparative example, and the results are shown in Table 1.
Embodiment 3
[0042] The production method of anti-oxidation polyamide reverse osmosis membrane is as follows:
[0043] 1. Preparation of aqueous phase liquid: same as comparative example.
[0044] 2. The preparation of the oil phase solution: the same as the comparative example.
[0045] 3. Preparation of post-grafting treatment solution: Weigh 8 g of succinic dialdehyde and add it to 1991 g of deionized water. After stirring for 5 minutes, add 1 g of tannic acid, and continue stirring for 10 minutes to obtain a post-grafting treatment solution.
[0046] 4, film making method is the same as embodiment 1
PUM
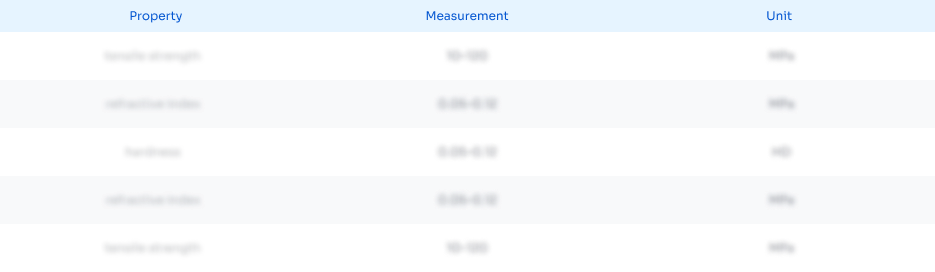
Abstract
Description
Claims
Application Information

- Generate Ideas
- Intellectual Property
- Life Sciences
- Materials
- Tech Scout
- Unparalleled Data Quality
- Higher Quality Content
- 60% Fewer Hallucinations
Browse by: Latest US Patents, China's latest patents, Technical Efficacy Thesaurus, Application Domain, Technology Topic, Popular Technical Reports.
© 2025 PatSnap. All rights reserved.Legal|Privacy policy|Modern Slavery Act Transparency Statement|Sitemap|About US| Contact US: help@patsnap.com