Grinding wheel route generation method for low-speed servo grinding of free-form surface
A path generation and grinding wheel technology, which is applied to the parts of grinding machine tools, grinding frame, grinding bed, etc., can solve the problems of deterioration of processing quality, time-consuming processing, and no calculation method of grinding wheel grinding path, etc. Achieve the effects of high processing efficiency, high processing surface precision, and guaranteed stability
- Summary
- Abstract
- Description
- Claims
- Application Information
AI Technical Summary
Problems solved by technology
Method used
Image
Examples
Embodiment approach 1
[0046] The structural layout of the machine tool in this embodiment is as follows: figure 1 As shown, the grinding wheel adopts a vertical structure. During processing, the workpiece 15 is adsorbed on the vacuum chuck 14, and is driven by the workpiece spindle (i.e., the C axis) to perform an angle-controllable rotary motion. The annular grinding wheel 17 is driven by the high-speed grinding spindle 16 to perform high-speed rotation, and the X-axis of the machine tool slides The plate 12 moves positively towards the X-axis, and the Z-axis sliding plate 18 performs feed motion with the rotation of the C-axis and the movement of the X-axis under the control of the machining program, so that the grinding process of the free-form surface can be realized. Among them, planning the relationship between the movement of the X and Z axes and the rotation angle of the C axis according to the geometric parameters of the free-form surface and the grinding wheel is a key issue in ultra-prec...
Embodiment approach 2
[0063] The structural layout of the machine tool in this embodiment is as follows: Figure 5 As shown, the grinding wheel adopts a horizontal structure. During processing, the workpiece 57 is adsorbed on the vacuum chuck 58, and is driven by the workpiece spindle (i.e., the C axis) to perform an angle-controllable rotary motion. The annular grinding wheel 56 is driven by the high-speed grinding spindle 54 to perform high-speed rotation, and the X-axis of the machine tool slides The plate 53 moves in the positive direction of the X-axis, and the Z-axis sliding plate 55 performs a feed motion with the rotation of the C-axis and the movement of the X-axis under the control of the machining program, so that the grinding process of the free-form surface can be realized. Among them, planning the relationship between the movement of the X and Z axes and the rotation angle of the C axis according to the geometric parameters of the free-form surface and the grinding wheel is a key issu...
Embodiment 1
[0080] freeform surface
[0081]
[0082] For example, using the method of Embodiment 1 to plan the machining path of the free-form surface, the geometric parameters of the annular grinding wheel are R=11 mm, r=1 mm, and the pitch of the equidistant helix is set to 1 mm. The corresponding relationship between the generated tool control point X coordinate and Z coordinate and the rotation angle θ is as follows: Figure 8 As shown, the dotted line in the figure represents the X coordinate of the tool control point, and the solid line represents the Z coordinate.
PUM
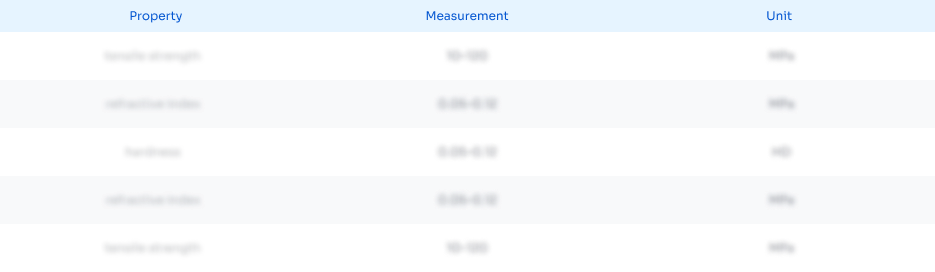
Abstract
Description
Claims
Application Information

- R&D
- Intellectual Property
- Life Sciences
- Materials
- Tech Scout
- Unparalleled Data Quality
- Higher Quality Content
- 60% Fewer Hallucinations
Browse by: Latest US Patents, China's latest patents, Technical Efficacy Thesaurus, Application Domain, Technology Topic, Popular Technical Reports.
© 2025 PatSnap. All rights reserved.Legal|Privacy policy|Modern Slavery Act Transparency Statement|Sitemap|About US| Contact US: help@patsnap.com