Light beam-electron beam composite brazing method for high-nitrogen steel
A technology of electron beam and high-nitrogen steel, which is applied in the direction of welding medium, welding equipment, welding/cutting medium/material, etc., can solve the problems of reducing the comprehensive performance of welding joints, weakening material performance, and large deformation of welding surface, etc., to overcome air holes Disadvantages, weakened grain growth, and good welding quality
- Summary
- Abstract
- Description
- Claims
- Application Information
AI Technical Summary
Problems solved by technology
Method used
Image
Examples
Embodiment 1
[0031] For 0.9 parts of N, 65 parts of Fe, 1.9 parts of Ni, 23 parts of Cr, 19 parts of Mn, 1.2 parts of Mo, 0.2 parts of C, 0.02 parts of S, 0.05 parts of P and 0.5 parts of Si (by weight) The steel is brazed, and first prepared is composed of 25 parts of Pd, 46 parts of Ni, 36 parts of Cr, 2.8 parts of vanadium-nickel-coated graphene, 12 parts of Mn, 7 parts of Re, 6 parts of Si and 2 parts of B (by weight). The brazing paste, the specific preparation method of this solder paste is as follows:
[0032] The first step, utilize FAD5001 electronic balance, weigh 15g distilled water, 15g water-based binder, molar concentration be 15.97mol / L alcohol 6g and 5g acetone, above-mentioned water-based binder is made of zinc phosphate 36 weight parts, chlorinated 45 parts by weight of ammonium, 15 parts by weight of polyethylene glycol, 14 parts by weight of butyl cyanoacrylate, and 11 parts by weight of ammonium persulfate; meanwhile, configure Pd, Ni, Cr, vanadium-nickel graphene, Mn,...
Embodiment 2
[0043] For 2.1 parts of N, 51 parts of Fe, 2.7 parts of Ni, 28 parts of Cr, 25 parts of Mn, 1.6 parts of Mo, 0.6 parts of C, 0.05 parts of S, 0.08 parts of P and 0.8 parts of Si (by weight) The steel is brazed, first prepared by 28 parts of Pd, 39 parts of Ni, 39 parts of Cr, 5.8 parts of vanadium-nickel-coated graphene, 15 parts of Mn, 11 parts of Re, 9 parts of Si and 5.5 parts of B (by weight). The brazing paste, the specific preparation method of this solder paste is as follows:
[0044] The first step, utilize FAD5001 electronic balance, weigh 30g distilled water, 30g water-based binder, 13g molar concentration be the alcohol of 15.97mol / L and 12g acetone, above-mentioned water-based binder is made of 24 parts by weight of zinc phosphate, chlorine 61 parts by weight of ammonium chloride, 23 parts by weight of polyethylene glycol, 22 parts by weight of butyl cyanoacrylate, and 7 parts by weight of ammonium persulfate; meanwhile, configure Pd, Ni, Cr, vanadium-plated nickel...
Embodiment 3
[0054] For 1.5 parts of N, 58 parts of Fe, 2.3 parts of Ni, 25.5 parts of Cr, 22 parts of Mn, 1.4 parts of Mo, 0.4 parts of C, 0.035 parts of S, 0.065 parts of P and 0.65 parts of Si (by weight) The steel is brazed, first prepared by 26.5 parts of Pd, 42.5 parts of Ni, 37.5 parts of Cr, 4.3 parts of vanadium-nickel-coated graphene, 13.5 parts of Mn, 9 parts of Re, 7.5 parts of Si and 3.75 parts of B (by weight). The brazing paste, the specific preparation method of this solder paste is as follows:
[0055] The first step, utilizes FAD5001 electronic balance, weighs 22.5g distilled water, 22.5g water-based binder, 10.5g molar concentration is the alcohol of 15.97mol / L and 8.5g acetone, and above-mentioned water-based binder is made of zinc phosphate 30 weight parts, 53 parts by weight of ammonium chloride, 19 parts by weight of polyethylene glycol, 18 parts by weight of butyl cyanoacrylate, and 8 parts by weight of ammonium persulfate; meanwhile, configure Pd, Ni, Cr, vanadium-...
PUM
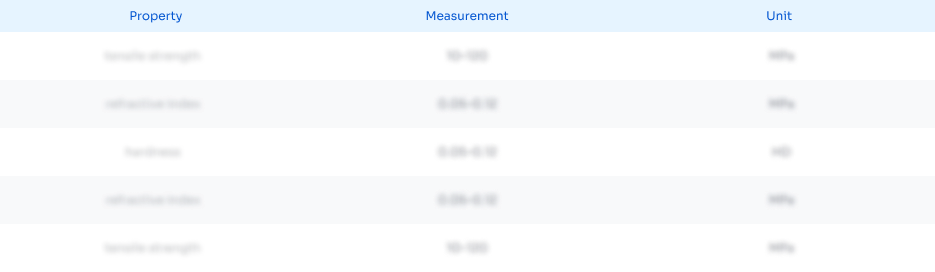
Abstract
Description
Claims
Application Information

- R&D Engineer
- R&D Manager
- IP Professional
- Industry Leading Data Capabilities
- Powerful AI technology
- Patent DNA Extraction
Browse by: Latest US Patents, China's latest patents, Technical Efficacy Thesaurus, Application Domain, Technology Topic, Popular Technical Reports.
© 2024 PatSnap. All rights reserved.Legal|Privacy policy|Modern Slavery Act Transparency Statement|Sitemap|About US| Contact US: help@patsnap.com