Electroslag remelting slag system and electroslag remelting 40CrNiMoA low-hydrogen control method
A technology of electroslag remelting and control method, which is applied in the field of electrometallurgy, can solve the problems of limited hydrogen diffusion effect, white spot caused by hydrogen content, affecting the performance of steel, etc., achieves excellent hydrogen reduction effect, reduces hydrogen source, The effect of energy saving and consumption reduction effect
- Summary
- Abstract
- Description
- Claims
- Application Information
AI Technical Summary
Problems solved by technology
Method used
Image
Examples
Embodiment 1
[0027] 1) Prepare electroslag remelting slag system, and its components are CaF in parts by weight 2 70 servings, Al 2 O 3 20 parts, SiO 2 6 parts, 4 parts of MgO, the alkalinity of the slag system B=0.84, weight 130kg;
[0028] 2) Bake the slag described in step 1) at 200°C for 4 hours, then at 800°C for 4 hours, take it out and use it immediately;
[0029] 3) Choose 40CrNiMoA electrode blank ∮400mm, clean the folds, slag inclusions, rust, etc. on the surface of the electrode blank, and the surface is sanded and bright, and the electrode blank is baked in a weak oxidizing atmosphere at 200°C for 3 hours; Weak oxidizing atmosphere includes CO, CO 2 And O 2 The mixed gas, the CO and CO 2 The total concentration of 30%, the O 2 The concentration is 5%.
[0030] 4) After assembling the electroslag remelting furnace, add step 2) the baked electroslag remelting slag to the crystallizer with an average diameter of ∮600mm. Adjust the voltage to 63V and the current to 12000A. Electroslag...
Embodiment 2
[0032] 1) Prepare electroslag remelting slag system, and its components are CaF in parts by weight 2 70 servings, Al 2 O 3 20 parts, SiO 2 6 parts, 4 parts of MgO, the alkalinity of the slag system B=0.84, weight 130kg;
[0033] 2) Bake the slag described in step 1) at 200°C for 4 hours, then at 800°C for 3 hours, take it out and use it immediately;
[0034] 3) Choose 40CrNiMoA electrode blank ∮400mm, clean the folds, slag inclusions, rust, etc. on the surface of the electrode blank, and the surface is sanded and bright, and the electrode blank is baked in a weak oxidizing atmosphere at 200°C for 3 hours; Weak oxidizing atmosphere includes CO, CO 2 And O 2 The mixed gas, the CO and CO 2 The total concentration is 35%, the O 2 The concentration is 8%.
[0035] 4) After assembling the electroslag remelting furnace, add step 2) the baked electroslag remelting slag to the crystallizer with an average diameter of ∮600mm. Adjust the voltage to 63V and the current to 12000A. Electroslag...
Embodiment 3
[0037] 1) Prepare electroslag remelting slag system, and its components are CaF in parts by weight 2 60 servings, Al 2 O 3 30 parts, SiO 2 5 parts, 5 parts of MgO, the alkalinity of the slag system B=0.9, weight 130kg
[0038] 2) Bake the slag described in step 1) at 240°C for 4 hours, then at 900°C for 3 hours, and take it out for immediate use;
[0039] 3) Choose 40CrNiMoA electrode blank ∮400mm, clean the folds, slag inclusions, rust, etc. on the surface of the electrode blank, and the surface is sanded and bright, and the electrode blank is baked in a weak oxidizing atmosphere at 200°C for 3 hours; Weak oxidizing atmosphere includes CO, CO 2 And O 2 The mixed gas, the CO and CO 2 The total concentration is 40%, the O 2 The concentration is 8%.
[0040] 4) After assembling the electroslag remelting furnace, add step 2) the baked electroslag remelting slag to the crystallizer with an average diameter of ∮600mm. Adjust the voltage to 63V and the current to 12000A. Electroslag re...
PUM
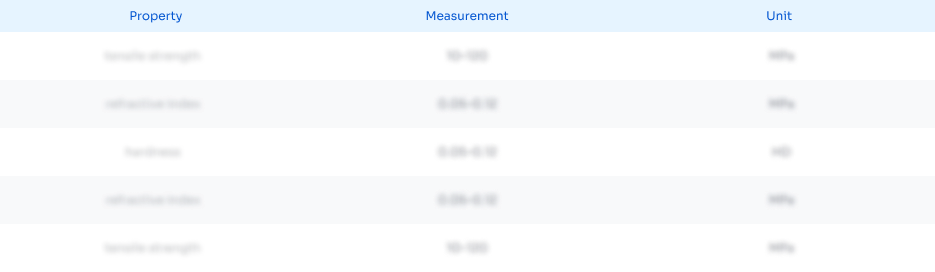
Abstract
Description
Claims
Application Information

- Generate Ideas
- Intellectual Property
- Life Sciences
- Materials
- Tech Scout
- Unparalleled Data Quality
- Higher Quality Content
- 60% Fewer Hallucinations
Browse by: Latest US Patents, China's latest patents, Technical Efficacy Thesaurus, Application Domain, Technology Topic, Popular Technical Reports.
© 2025 PatSnap. All rights reserved.Legal|Privacy policy|Modern Slavery Act Transparency Statement|Sitemap|About US| Contact US: help@patsnap.com