Combined treatment process of copper smelting electric dust acid leaching solution and arsenic sulfide slag
A technology for copper smelting and arsenic sulfide, which is applied in the field of combined treatment process of copper smelting electric dust ash acid leaching solution and arsenic sulfide slag, can solve the problems of high cost, restriction, and reduction of sulfur dioxide conversion rate, and achieve simple process flow and solution The effect of dealing with problems
- Summary
- Abstract
- Description
- Claims
- Application Information
AI Technical Summary
Problems solved by technology
Method used
Image
Examples
Embodiment 1
[0013] Embodiment 1: Copper smelting electric dust ash pickling solution and arsenic sulfide slag are taken as an example containing the following elements, and its element content is as shown in Table 1 and Table 2:
[0014] Table 1
[0015]
[0016] Table 2
[0017]
[0018] Take the following process steps:
[0019] a. Sizing and replacement: arsenic sulfide slag is slurried with copper smelting soot acid leaching solution, the molar ratio of copper and arsenic is controlled at 1.5:1, the temperature is 83°C, and the reaction is carried out under normal pressure for 2 hours to obtain copper sulfide slag and the liquid after replacement, and then vulcanized The copper grade in the copper slag is 61.96%, the arsenic grade is reduced to 0.1%, the arsenic content in the liquid after replacement is 13200mg / L, the copper content is reduced to 10 mg / L, and the copper slag is returned to the copper smelting system for ore blending treatment.
[0020] b. Sulfurization: After...
PUM
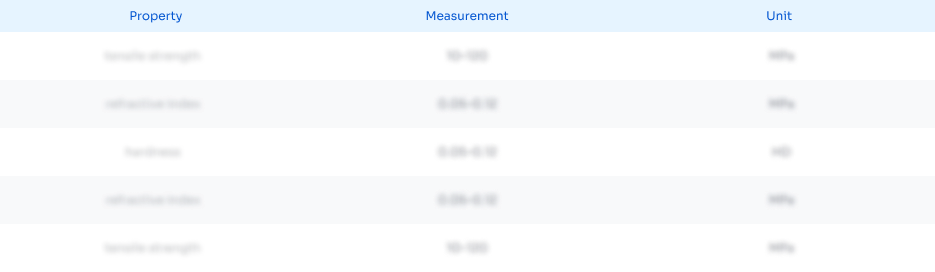
Abstract
Description
Claims
Application Information

- Generate Ideas
- Intellectual Property
- Life Sciences
- Materials
- Tech Scout
- Unparalleled Data Quality
- Higher Quality Content
- 60% Fewer Hallucinations
Browse by: Latest US Patents, China's latest patents, Technical Efficacy Thesaurus, Application Domain, Technology Topic, Popular Technical Reports.
© 2025 PatSnap. All rights reserved.Legal|Privacy policy|Modern Slavery Act Transparency Statement|Sitemap|About US| Contact US: help@patsnap.com