Fireproof door core and preparation method thereof
A technology of fire door core and polystyrene, which is applied in the field of fire door core, can solve the problems that affect the fire prevention, heat preservation and sound insulation effect of the board, poor dimensional stability and easy deformation, high energy consumption and environmental pollution, etc., and achieve good fire resistance and fire prevention effect , good thermal insulation effect, high dimensional stability
- Summary
- Abstract
- Description
- Claims
- Application Information
AI Technical Summary
Problems solved by technology
Method used
Image
Examples
Embodiment 1
[0031] A fire door core, comprising the following raw materials in parts by weight:
[0032] 16 parts of polystyrene fireproof particles, 3 parts of expanded vermiculite powder, 8 parts of polypropylene fiber, 6 parts of hollow glass microspheres, 10 parts of sepiolite fiber, 4 parts of diatomite, 4 parts of talcum powder, polyvinyl chloride paste resin 8 parts, water glass 12 parts, foaming agent 1 part, flame retardant 2 parts and silane coupling agent 1.2 parts.
[0033] The preparation method of polystyrene fireproof particles is as follows:
[0034] (1) Add polystyrene particles, nano-zinc oxide, nano-aluminum hydroxide and expanded graphite and an appropriate amount of γ-aminopropyltriethoxysilane to high-speed mixing and mix evenly, then add them to a twin-screw extruder to extrude After granulation, the pellets were placed in a dryer at 60 degrees Celsius and dried for 5 hours;
[0035] (2) Put polystyrene flame-retardant particles into a pre-expansion machine with a...
Embodiment 2
[0047] A fire door core, comprising the following raw materials in parts by weight:
[0048]22 parts of polystyrene fireproof particles, 7 parts of expanded vermiculite powder, 13 parts of polypropylene fiber, 11 parts of hollow glass microspheres, 17 parts of sepiolite fiber, 9 parts of diatomite, 9 parts of talcum powder, polyvinyl chloride paste resin 13 parts, 18 parts of water glass, 2 parts of foaming agent, 4 parts of flame retardant and 2.4 parts of silane coupling agent.
[0049] The preparation method of polystyrene fireproof particles is as follows:
[0050] (1) Add polystyrene particles, nano-zinc oxide, nano-aluminum hydroxide and expanded graphite and an appropriate amount of γ-aminopropyltriethoxysilane to high-speed mixing and mix evenly, then add them to a twin-screw extruder to extrude After granulation, the pellets were placed in a dryer at 70 degrees Celsius and dried for 5 hours;
[0051] (2) Put polystyrene flame-retardant particles into a pre-expansion...
Embodiment 3
[0063] A fire door core, comprising the following raw materials in parts by weight:
[0064] 18 parts of polystyrene fireproof particles, 4 parts of expanded vermiculite powder, 9 parts of polypropylene fiber, 7 parts of hollow glass microspheres, 12 parts of sepiolite fiber, 5 parts of diatomaceous earth, 5 parts of talcum powder, polyvinyl chloride paste resin 9 parts, water glass 14 parts, foaming agent 1.2 parts, flame retardant 2.5 parts and silane coupling agent 1.6 parts.
[0065] The preparation method of polystyrene fireproof particles is as follows:
[0066] (1) Add polystyrene particles, nano-zinc oxide, nano-aluminum hydroxide and expanded graphite and an appropriate amount of γ-aminopropyltriethoxysilane to high-speed mixing and mix evenly, then add them to a twin-screw extruder to extrude After granulation, the pellets were placed in a dryer at 62 degrees Celsius and dried for 5 hours;
[0067] (2) Put polystyrene flame-retardant particles into a pre-expansion ...
PUM
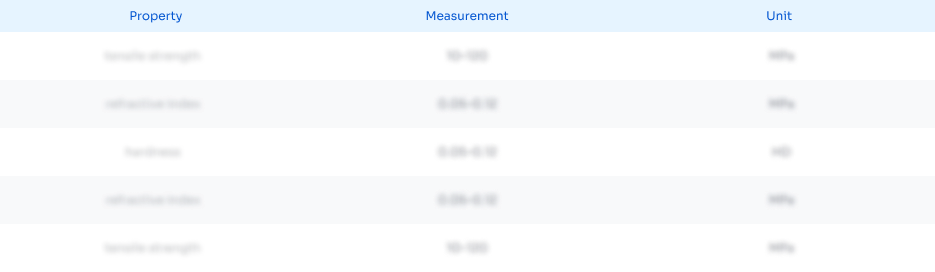
Abstract
Description
Claims
Application Information

- R&D Engineer
- R&D Manager
- IP Professional
- Industry Leading Data Capabilities
- Powerful AI technology
- Patent DNA Extraction
Browse by: Latest US Patents, China's latest patents, Technical Efficacy Thesaurus, Application Domain, Technology Topic, Popular Technical Reports.
© 2024 PatSnap. All rights reserved.Legal|Privacy policy|Modern Slavery Act Transparency Statement|Sitemap|About US| Contact US: help@patsnap.com