Precast concrete component exposed aggregate and preparation method thereof
A technology of prefabricated components and exposed aggregates is applied in the field of concrete prefabricated components, which can solve the problems of high production cost and complex components, and achieve the effects of improving corrosion resistance, simple components and reducing costs.
- Summary
- Abstract
- Description
- Claims
- Application Information
AI Technical Summary
Problems solved by technology
Method used
Image
Examples
preparation example Construction
[0047] The road aggregate of the above-mentioned concrete prefabricated component needs to be mixed with various raw materials. The preparation method is simple, and the preparation method includes the following steps:
[0048] S1: Weigh the following raw materials according to the mass percentage:
[0049] Sodium gluconate 7.5% to 10%, thickener 0.8% to 1.2%, preservative 0.1% to 0.5%, water 88.3% to 91.6%; the sum of the mass percentages of the above components is 100%; among them, the thickener is Hydroxypropyl methylcellulose, preservative is sodium benzoate, water is drinking water.
[0050] S2: Add the sodium gluconate weighed in step S1 to the water weighed in step S1 for the first stirring, because sodium gluconate is easily soluble in water, just stir at a low speed, the stirring speed of the first stirring is 300r / min~ 500r / min, sodium gluconate is dissolved completely, obtains sodium gluconate solution; Add the thickener that step S1 takes by weighing in described ...
Embodiment 1
[0056] Weigh respectively 7.5% of sodium gluconate, 0.8% of hydroxypropyl methylcellulose, 0.1% of sodium benzoate, and 91.6% of drinking water according to mass percentage, add sodium gluconate to drinking water and stir for the first time, stir for the first time The speed is 500r / min to completely dissolve sodium gluconate to obtain a sodium gluconate solution; add hydroxypropyl methylcellulose to hot water at a temperature of 60°C to dissolve part of it in advance, and the mass ratio of thickener to hot water The ratio is 1:13, to obtain the mixed solution c, then add the mixed solution c to the sodium gluconate solution for the second stirring, until the hydroxypropyl methylcellulose is completely dissolved, to obtain the mixed solution a, continue to add the mixed solution a Sodium benzoate was added to the mixture, stirred for the third time to obtain the mixed solution b, and then the mixed solution b was left to stand for 24 hours to obtain the finished product A with ...
Embodiment 2
[0058] Weigh respectively 8.5% of sodium gluconate, 1.0% of hydroxypropyl methylcellulose, 0.5% of sodium benzoate, and 90.0% of drinking water according to mass percentage, add sodium gluconate to drinking water and stir for the first time, stir for the first time The speed is 450r / min to completely dissolve sodium gluconate to obtain a sodium gluconate solution; add hydroxypropyl methylcellulose to hot water at a temperature of 55°C to dissolve part of it in advance, and the mass ratio of thickener to hot water The ratio is 1:12 to obtain the mixed solution c, then add the mixed solution c to the sodium gluconate solution for the second stirring until the hydroxypropyl methylcellulose is completely dissolved to obtain the mixed solution a, and continue to add the mixed solution to the mixed solution a Sodium benzoate was added to the mixture, stirred for the third time to obtain the mixed solution b, and then the mixed solution b was left to stand for 24 hours to obtain the f...
PUM
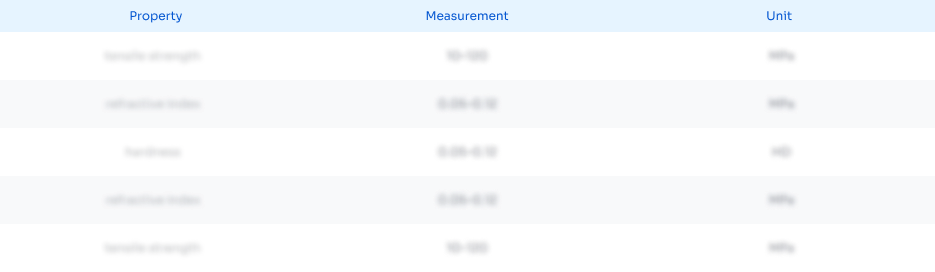
Abstract
Description
Claims
Application Information

- R&D
- Intellectual Property
- Life Sciences
- Materials
- Tech Scout
- Unparalleled Data Quality
- Higher Quality Content
- 60% Fewer Hallucinations
Browse by: Latest US Patents, China's latest patents, Technical Efficacy Thesaurus, Application Domain, Technology Topic, Popular Technical Reports.
© 2025 PatSnap. All rights reserved.Legal|Privacy policy|Modern Slavery Act Transparency Statement|Sitemap|About US| Contact US: help@patsnap.com