Machining and positioning combination fixture for thin-walled part with threaded hole
A technology of thin-walled parts and threaded holes, which is applied in the field of parts processing and positioning tooling and fixtures, can solve the problems of processing accuracy, coaxiality and taper runout, which are difficult to meet processing requirements, easy to crush threads, and difficult to clamp. Achieve good economical practicability and popularization, improve machining accuracy and coaxiality, and facilitate and quick installation.
- Summary
- Abstract
- Description
- Claims
- Application Information
AI Technical Summary
Problems solved by technology
Method used
Image
Examples
Embodiment Construction
[0016] The following will clearly and completely describe the technical solutions in the embodiments of the present invention in conjunction with the accompanying drawings in the embodiments of the present invention:
[0017] like Figure 1~Figure 3 As shown, a combination fixture for machining and positioning of thin-walled parts with threaded holes is used for clamping and positioning of thin-walled parts 2 such as pipe sleeves. The axis of the thin-walled parts 2 is provided with a threaded through hole, which includes Specifically 1 and the expansion body 3, the expansion body 3 is screwed into the clamp body 1, specifically, the clamp body 1 is a limit end 11 and a clamping rod 12 of an integral structure made of spring steel Composition, the clamping rod 12 is a hollow structure, the outer surface of the clamping rod 12 is provided with external threads that match the threaded holes of the thin-walled parts 2, preferably, the outer diameter of the thread on the outer sur...
PUM
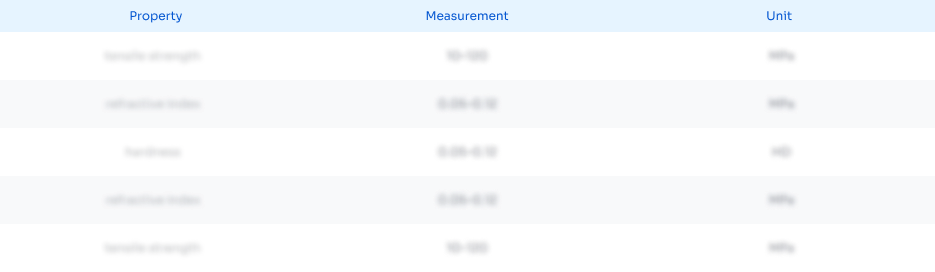
Abstract
Description
Claims
Application Information

- R&D
- Intellectual Property
- Life Sciences
- Materials
- Tech Scout
- Unparalleled Data Quality
- Higher Quality Content
- 60% Fewer Hallucinations
Browse by: Latest US Patents, China's latest patents, Technical Efficacy Thesaurus, Application Domain, Technology Topic, Popular Technical Reports.
© 2025 PatSnap. All rights reserved.Legal|Privacy policy|Modern Slavery Act Transparency Statement|Sitemap|About US| Contact US: help@patsnap.com