Repairing method of surface scratches of shaft sleeve of connecting shaft of helicopter
A technology for connecting shafts and helicopters, applied in the field of repairing scratches on the surface of shaft sleeves, can solve the problems of helicopter safety hazards, cost waste, stress concentration, etc., and achieve the effects of improving corrosion resistance, reducing scrap costs, and eliminating stress concentration
- Summary
- Abstract
- Description
- Claims
- Application Information
AI Technical Summary
Problems solved by technology
Method used
Image
Examples
Embodiment
[0026] The bushing of the 001# connecting shaft of a certain type of helicopter has a scratch at a position 60mm away from the side end face of the main reducer. The scratch depth is 0.1mm, the length is about 5mm, and the width is about 4mm. The repair steps are as follows:
[0027] (1) Disassemble the faulty bushing, the defective position is located 60mm from the end face of the main reducer, and repair it according to step (2);
[0028] (2) The depth e of the surface defect is 0.1mm, and repaired according to the step (3);
[0029] (3) Use 300-mesh sandpaper to perform smooth transition treatment on the defect position within the range of radius R=5mm, and the grinding depth is 0.15mm;
[0030] (4) Alodin treatment is carried out on the polished part, and the coating surface is continuous, uniform and streak-free and does not expose the shaft sleeve substrate;
[0031] (5) The quality of the Alodine coating meets the requirements, and the step (6) is performed;
[0032] ...
PUM
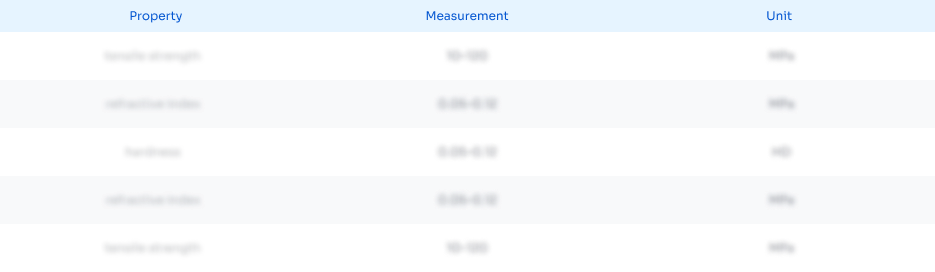
Abstract
Description
Claims
Application Information

- R&D
- Intellectual Property
- Life Sciences
- Materials
- Tech Scout
- Unparalleled Data Quality
- Higher Quality Content
- 60% Fewer Hallucinations
Browse by: Latest US Patents, China's latest patents, Technical Efficacy Thesaurus, Application Domain, Technology Topic, Popular Technical Reports.
© 2025 PatSnap. All rights reserved.Legal|Privacy policy|Modern Slavery Act Transparency Statement|Sitemap|About US| Contact US: help@patsnap.com