Coupling method for waterborne epoxy coating and graphene oxide composite coating interfacial hyperbranched polyamide
A technology of hyperbranched polyamide and water-based epoxy coatings, applied in epoxy resin coatings, coatings, etc., can solve the problems of insignificant effect and weak pertinence, and achieves improved interface chemical reaction, improved dispersion performance, and improved water resistant effect
- Summary
- Abstract
- Description
- Claims
- Application Information
AI Technical Summary
Problems solved by technology
Method used
Examples
Embodiment 1
[0016] First, take 5 grams of graphene oxide and 52 grams of diethylenetriamine and mix them evenly, ultrasonically disperse them for more than 20 minutes, add them into a three-necked flask equipped with a stirrer, slowly add 50 grams of succinic anhydride, and react at about 50°C for 1 hour, Nitrogen protection, stop stirring, heat up to 130 degrees to melt polycondensation reaction for more than 3 hours, cool down to about 90 degrees, add water to form a dispersion, centrifuge, wash, and configure 1% of graphene oxide grafted with hyperbranched polyamide in situ Concentrated dispersion, spare. Then, weigh the water-based epoxy emulsion and curing agent according to the epoxy equivalent and active hydrogen equivalent 1:1, add graphene oxide grafted with hyperbranched polyamide at a mass ratio of 0.2%, stir evenly, spray on the tinplate, and dry completely at room temperature Test performance. Compared with the graphene oxide grafted hyperbranched polyamide, the water resist...
Embodiment 2
[0018] First, take 5 grams of graphene oxide and 52 grams of diethylenetriamine and mix them evenly, ultrasonically disperse them for more than 20 minutes, add them into a three-necked flask equipped with a stirrer, slowly add 50 grams of succinic anhydride, and react at about 50°C for 1 hour, Nitrogen protection, stop stirring, heat up to 130 degrees to melt polycondensation reaction for more than 3 hours, cool down to about 90 degrees, add water to form a dispersion, centrifuge, wash, and configure 1% of graphene oxide grafted with hyperbranched polyamide in situ Concentrated dispersion, spare. Then, weigh the water-based epoxy emulsion and curing agent according to the epoxy equivalent and active hydrogen equivalent 1:1, add graphene oxide grafted with hyperbranched polyamide at a mass ratio of 0.5%, stir evenly, spray on the tinplate, and dry completely at room temperature Test performance. Compared with the graphene oxide grafted hyperbranched polyamide, the water resist...
Embodiment 3
[0020] First, take 5 grams of graphene oxide and 73 grams of polyethylene polyamine and mix evenly, ultrasonically disperse for more than 20 minutes, add it to a three-necked flask equipped with a stirrer, slowly add 50 grams of succinic anhydride, and react at about 50 ° C for 1 hour, Nitrogen protection, stop stirring, heat up to 130 degrees to melt polycondensation reaction for more than 3 hours, cool down to about 90 degrees, add water to form a dispersion, centrifuge, wash, and configure 1% of graphene oxide grafted with hyperbranched polyamide in situ Concentrated dispersion, spare. Then, weigh the water-based epoxy emulsion and curing agent according to the epoxy equivalent and active hydrogen equivalent 1:1, add graphene oxide grafted with hyperbranched polyamide at a mass ratio of 0.5%, stir evenly, spray on the tinplate, and dry completely at room temperature Test performance. Compared with graphene oxide grafted hyperbranched polyamide, the water resistance, salt w...
PUM
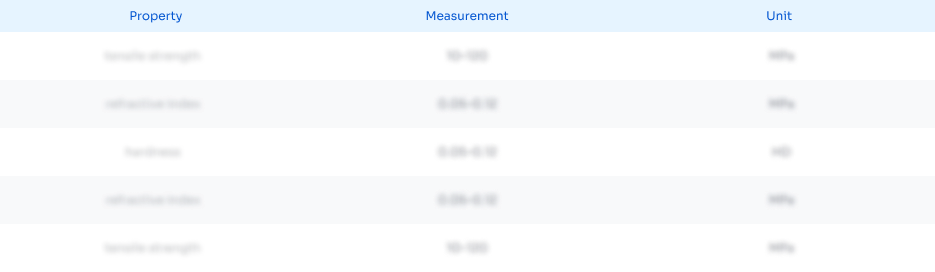
Abstract
Description
Claims
Application Information

- R&D Engineer
- R&D Manager
- IP Professional
- Industry Leading Data Capabilities
- Powerful AI technology
- Patent DNA Extraction
Browse by: Latest US Patents, China's latest patents, Technical Efficacy Thesaurus, Application Domain, Technology Topic, Popular Technical Reports.
© 2024 PatSnap. All rights reserved.Legal|Privacy policy|Modern Slavery Act Transparency Statement|Sitemap|About US| Contact US: help@patsnap.com