Efficient laser drilling and cleaning optical system
A laser drilling and optical system technology, applied in the field of laser scanning, can solve the problems of restricting the efficiency of laser drilling and laser cleaning, and achieve the effect of improving the effective reflection area, reducing the quality, and overcoming the large and bulky
- Summary
- Abstract
- Description
- Claims
- Application Information
AI Technical Summary
Problems solved by technology
Method used
Image
Examples
Embodiment 1
[0025] A high-efficiency laser drilling and cleaning optical system, comprising a housing 10, an upper cover, an optical fiber collimator coupler 1 arranged outside the housing 10, a coupler flange 2, a field lens assembly 7, an electrical connector 9, and a device Beam expander assembly 3, reflector assembly 4, polygon mirror assembly 6, motor assembly 5, photoelectric switch assembly 8 in described shell 10; Described optical fiber collimating coupler 1 is connected to by described coupler flange 2 On the side of the housing 10, the beam expander assembly 3 is arranged in the laser incident direction of the fiber collimator coupler 1, and the reflector assembly 4 is arranged in the laser incident direction of the beam expander assembly 3 , and reflect the laser light to the polygon mirror assembly 6; the motor assembly 5 is connected to the polygon mirror assembly 6 to drive the rotation of the polygon mirror assembly 6, and the field lens assembly 7 is arranged on the polygo...
Embodiment 2
[0029] On the basis of Embodiment 1, the beam expander assembly 3 includes a beam expander bracket 31 and a beam expander 32, the beam expander bracket 31 is arranged on the bottom surface of the housing 10, and its upper part is provided with a threaded through hole, The beam expander 32 is connected in the threaded through hole. The structure is convenient for installation, disassembly and maintenance. The main axis of the beam expander 32 coincides with the optical axis of the laser to expand the laser beam so as to obtain a small-diameter spot on the focal plane of the field lens.
[0030] The reflector assembly 4 includes a reflector bracket 41, a reflector and a mirror pressure ring 43. The reflector bracket 41 is arranged on the bottom surface of the housing 10, and its upper part is provided with a counterbore, and the inner side wall of the counterbore is provided with There is an internal thread, the reflector is arranged in the counterbore, and the outside of the re...
PUM
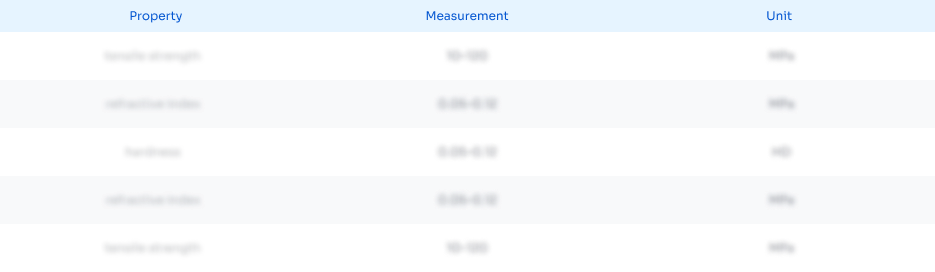
Abstract
Description
Claims
Application Information

- R&D
- Intellectual Property
- Life Sciences
- Materials
- Tech Scout
- Unparalleled Data Quality
- Higher Quality Content
- 60% Fewer Hallucinations
Browse by: Latest US Patents, China's latest patents, Technical Efficacy Thesaurus, Application Domain, Technology Topic, Popular Technical Reports.
© 2025 PatSnap. All rights reserved.Legal|Privacy policy|Modern Slavery Act Transparency Statement|Sitemap|About US| Contact US: help@patsnap.com