Numerical control grinding and finishing method for blade shot peening surface
A finishing and grinding technology, used in metal processing equipment, abrasives, manufacturing tools, etc., can solve problems such as small material removal, achieve uniform coverage, avoid overheating, and avoid overcutting.
- Summary
- Abstract
- Description
- Claims
- Application Information
AI Technical Summary
Problems solved by technology
Method used
Image
Examples
Embodiment 1
[0038] on a six-coordinate linkage CNC abrasive belt grinder figure 1 The surface of the airfoil in the "SA" region and the shot-peened surface of the blade root fillet transition zone in the "SB" region are ground and finished separately. Through the optimal design of the contact wheel, the selection of finishing tools and cooling methods, as well as the optimization and processing of the program, the research of key grinding parameters such as speed, feed, contact force and step distance can meet different types of blade profiles. Residual compressive stress and roughness design requirements. The specific steps are as follows:
[0039] 1.1 Smoothing the root fillet transition area
[0040] 1.1.1 will be as figure 2 The nylon polishing wheel shown is rounded R2~R3, and installed on the abrasive belt grinder after completion;
[0041] 1.2.2 If image 3As shown, the nylon wheel 1 reciprocally moves along the chord width direction of the blade shape to smooth the transitio...
Embodiment 2
[0046] on a six-coordinate linkage CNC abrasive belt grinder figure 1 The surface of the airfoil in the "SA" region and the shot-peened surface of the blade root fillet transition zone in the "SB" region are ground and finished separately. Through the optimal design of the contact wheel, the selection of finishing tools and cooling methods, as well as the optimization and processing of the program, the research of key grinding parameters such as speed, feed, contact force and step distance can meet different types of blade profiles. Residual compressive stress and roughness design requirements. The specific steps are as follows:
[0047] 1.1 Smoothing the root fillet transition area
[0048] 1.1.1 will be as figure 2 The nylon polishing wheel shown is rounded R2~R3, and installed on the abrasive belt grinder after completion;
[0049] 1.2.2 If image 3 As shown, the nylon wheel 1 reciprocates along the chord width direction of the blade shape to smooth the transition are...
PUM
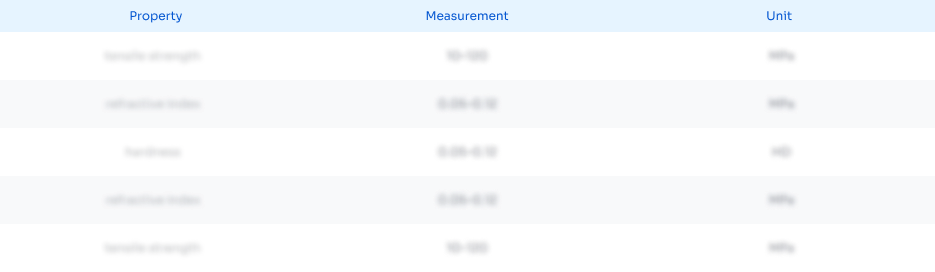
Abstract
Description
Claims
Application Information

- Generate Ideas
- Intellectual Property
- Life Sciences
- Materials
- Tech Scout
- Unparalleled Data Quality
- Higher Quality Content
- 60% Fewer Hallucinations
Browse by: Latest US Patents, China's latest patents, Technical Efficacy Thesaurus, Application Domain, Technology Topic, Popular Technical Reports.
© 2025 PatSnap. All rights reserved.Legal|Privacy policy|Modern Slavery Act Transparency Statement|Sitemap|About US| Contact US: help@patsnap.com